Employee Instability and Company Profits
How investing in your workforce creates employer stability.
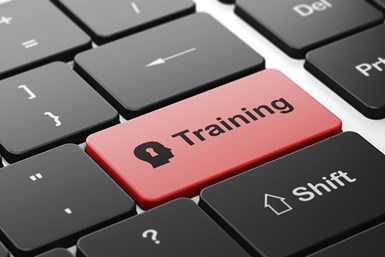
Employers are constantly looking for ways to increase productivity and motivation while improving the bottom line. Over the years, I have read a couple of books on how investing in your workforce creates employer stability.
In by Zeynep Ton, Ton shows how operational excellence calls for sustainable wages, employee benefits, and nonerratic schedules. Ton writes that you can pay a livable wage with benefits and still keep costs and prices low. She references the successful 911±¬ÁÏÍø practices of a handful of companies that have chosen to make employees a top priority and are recognizing lower costs, higher profits, and greater customer satisfaction.
Jody Heymann, in , demonstrates through various examples that if you invest in your entry-level, lower-wage employees, you will see lower costs, increased profits, less turnover, and higher motivation.
In addition, my book, , argues that by understanding the environments of employees who live in daily instability and daily stability and how individuals in each environment spend their time, you can better support your employees, which in turn supports and stabilizes your 911±¬ÁÏÍø.
What can life (or a typical day) look like for one who lives in daily instability? In previous blog posts, I have defined daily instability as not having resources for today, let alone for tomorrow. When an employee lives in this type of environment, the mindset is about making it through the day; solving today’s problems; relying on relationships with neighbors, families, and tribe; and just plain survival.
Such a life is characterized by a combination of multiple jobs (not careers), transportation issues, childcare issues, elder support, irregular and possibly inconsistent hours, and appointments with agencies that support families with food, utility, housing, physical and mental health, and safety needs. Now, do you have a better understanding of why life might get in the way of work? The question then becomes: What supports can a 911±¬ÁÏÍø provide that stabilize employees while also stabilizing the company? How can we do 911±¬ÁÏÍø differently to get the desired results we are looking for?
In the Workplace Stability workshop, we discuss what solutions there might be to address food insecurity, transportation, childcare, benefits, and more. Are we asking you to lower your standards? No. But by making changes for this employee demographic, you will find that you stabilize your 911±¬ÁÏÍø, as well as your employees.
This employee demographic is not going to change. Finding ways to stabilize and leverage your diverse workforce can be a major competitive advantage. While other 911±¬ÁÏÍøes stay on the hire/fire treadmill, you can boost profits and productivity by redesigning the way you do 911±¬ÁÏÍø. Based on employee demographics and the employees who are available for hiring, it is in our best interest to invest in our workforce, particularly our entry-level, lower-wage employees. This investment will stabilize your employee base, reduce hiring and training costs, improve morale and retention, and increase profits.
About the Author: Ruth K. Weirich, MBA, is an author, trainer, and management professional experienced in 911±¬ÁÏÍø operations efficiency and profitability. She is also a past president of aha! Process, an education and training company specializing in economic class issues. Contact: rkweirich@ahaprocess.com; .
Related Content
Educational Grant and Student Scholarships Open
The Society of Plastics Engineers’ Mold Technologies division is accepting applications for a $5,000 educational grant and a new $3,000 student scholarship honoring Glenn Beall.
Read MoreIn-Person Training Course Tackles Plastics Material Selection
The Madison Group plastics consultancy has created a two-and-a-half day in-person course to be held in Minneapolis that aims to help attendees develop a systematic and optimized approach to plastic material selection.
Read MoreKraussMaffei and NIAR Propel Injection Molded Thermoplastic Composites
The maker of plastics processing equipment has placed a machine and an injection molding expert in NIAR’s ATLAS lab in Wichita, Kansas, to help molding, composites and aerospace take off.
Read MoreCommunity College Launches Injection Molding Bootcamp
Nebraska’s Central Community College, which has become a centrally located training hub, successfully launched a plastics bootcamp this summer, boosting available workforce for regional molders.
Read MoreRead Next
Making the Circular Economy a Reality
Driven by brand owner demands and new worldwide legislation, the entire supply chain is working toward the shift to circularity, with some evidence the circular economy has already begun.
Read MoreFor PLASTICS' CEO Seaholm, NPE to Shine Light on Sustainability Successes
With advocacy, communication and sustainability as three main pillars, Seaholm leads a trade association to NPE that ‘is more active today than we have ever been.’
Read MoreBeyond Prototypes: 8 Ways the Plastics Industry Is Using 3D Printing
Plastics processors are finding applications for 3D printing around the plant and across the supply chain. Here are 8 examples to look for at NPE2024.
Read More