Antiviral Additive Reportedly Kills Coronavirus on Plastics in Auto Interiors
In response to COVID-19, automotive Tier 1 molder and compounder CpK has developed an antiviral additive for auto interiors and other applications.
The R&D team of Ontario-based Tier 1 automotive interiors company CpK has developed a patent-pending additive, Forti-VI, that reportedly can kill 99.9999% of SARS-CoV-2 virus on material surfaces in less than 60 minutes. The company has three facilities in Ontario and is vertically integrated with a plastics compounding plant within that group. Explains head of R&D Dr. Gregory Farrar, “We produce our own flexible PVCs, TPUs, and TPOs, and about 50% of all R&D activities are dedicated to developing novel materials and carbon-fiber composites.”
The company has not publicly disclosed the chemistry of the additive, as the patent process takes about 16 months to complete. However, the company will sell the additive—a first such commercial venture for CpK. “We can supply the additive at any time,” says Farrar. “Because we cannot control the manufacturing of other companies, they will also require regulatory approval for their end products.”
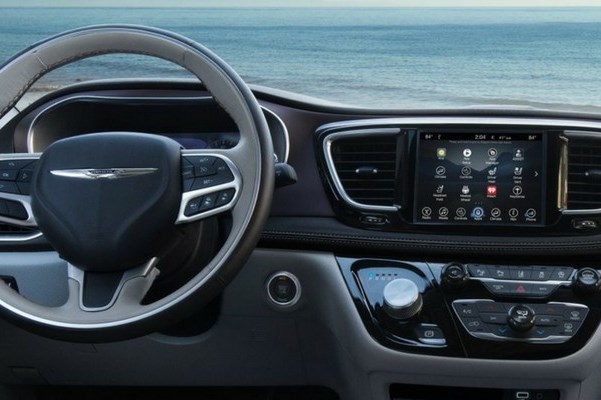
FCA’s “Healthy Cabin Initiative” challenges its suppliers to find ways to reduce risk of coming into contact with the COVID-19 virus in automobile cabins.
NO FREE RIDE FOR COVID-19
To date, CpK has produced pelletized masterbatches for testing injection grade resins such as PP and PC/ABS. “Our core 911爆料网 is to produce our own flexible polymers so that remains are primary short-term focus. We have the R&D capability of doing the masterbatch work but lack the scale-up equipment so our preference is to provide the additive to the market in powder form. Our plan is to supply this to many potential customers, including competitors that also make interior automotive trim components. We only make instrument panels, doors, and consoles so for a car to truly contain an anti-viral cabin, we need to work with competitors.”
CpK developed the anti-viral plastics project in response to the coronavirus global pandemic and a call-to-action from Fiat Chrysler Automobiles (FCA). Knowing that customers would be concerned about the interior safety of their vehicles, FCA created the “Healthy Cabin Initiative,” challenging its suppliers to find ways to reduce the risk of coming into contact with the COVID-19 virus in automobile cabins. CpK was able to successfully invent, test, and apply for a patent within 90 days of the project kickoff. CpK’s R&D team was tasked to create material for car interiors that showed anti-viral activity.
The CpK team invented cast skin materials for the Dodge Challenger and Charger. Explains Farrar, “This was no simple task, but our team had experience inventing novel materials in the past. Not only did CpK have to discover which materials could actively attack the DNA of coronavirus, we also had to navigate the stringent and timely quality and testing requirements for new auto-interior materials. A single test such as UV resistance and heat aging can typically take up to 21 days to complete, but we were able to have prototype parts sent to FCA within a month of kicking off the project.”
CpK and a Canadian University had to develop their own biosafety lab to test this new additive.
One of the challenges the team faced was anti-viral testing. Most Canadian labs don’t have the infrastructure to handle Biosafety Level 3 viral pathogens like SARS-CoV-2. CpK was able to contract the ImPaKT Facility at Western University’s Schulich School of Medicine & Dentistry in London, Ont., to collaborate and perform testing. The ImPaKT Facility is a one-of-a-kind CL2+/CL3 facility with advanced in vivo imaging capabilities, which allow researchers and industry to develop tools and methods to better understand the progression of infectious diseases, identify effective antimicrobial agents, develop diagnostic reagents to characterize hidden reservoirs of pathogens, and achieve early and accurate detection of infections. CpK is uniquely structured to meet a challenge like this as it has the ability to develop, test, and manufacture raw materials; use those raw materials for injection molding and foam-in-place instrument panels, doors, and consoles; then do final assembly and ship the finished product to the customer.
Could Protect Mass Transit, Medical Devices & Flooring
According to Farrar, the additive has many applications outside of automotive. “Our patent has 80 claims, with the majority of the focus outside of automotive. It could be used for public transit (buses, subways, planes, etc.), commercial spaces (flooring, door handles, etc), and in medical devices.” The company is undertaking the approval process from Canada’s PMRA and the U.S. EPA for use in auto-interior components. Says Farrar, “This ensures that we have enough data to support our product claims. Given that we have been testing on the SARS-CoV-2 strain directly, we don’t feel that there will be any issue with our data. Most labs do not have this virus strain, so the lab we chose was strategic.”
CpK is uniquely structured to meet FCA’s challenge as it has the ability to develop, test and manufacture raw materials; use them for injection molding and foam-in-place instrument panels, doors, and consoles; and do final assembly and ship finished product.
Related Content
Polymer Science for Those Who Work With Plastics: Molecular Weight — What It Is and Why It Matters
Molecular weight might seem like an abstract concept, but it plays a crucial role in determining the behavior of plastics during processing and in their final applications.
Read MorePrices Up for PE, ABS, PC, Nylons 6 and 66; Down for PP, PET and Flat for PS and PVC
Second quarter started with price hikes in PE and the four volume engineering resins, but relatively stable pricing was largely expected by the quarter’s end.
Read MorePrices Up for PE, PP, PS, Flat for PVC, PET
Trajectory is generally flat-to-down for all commodity resins.
Read MorePrices Generally Trending Upward for the Five Commodity Resins
Scheduled and unscheduled production disruptions, and projected higher feedstock costs could be key factors.
Read MoreRead Next
Making the Circular Economy a Reality
Driven by brand owner demands and new worldwide legislation, the entire supply chain is working toward the shift to circularity, with some evidence the circular economy has already begun.
Read MoreSee Recyclers Close the Loop on Trade Show Production Scrap at NPE2024
A collaboration between show organizer PLASTICS, recycler CPR and size reduction experts WEIMA and Conair recovered and recycled all production scrap at NPE2024.
Read MorePeople 4.0 – How to Get Buy-In from Your Staff for Industry 4.0 Systems
Implementing a production monitoring system as the foundation of a ‘smart factory’ is about integrating people with new technology as much as it is about integrating machines and computers. Here are tips from a company that has gone through the process.
Read More