Extruder Alignment: Important, but Only Half the Equation
The other half? Aligning and supporting downstream equipment. Here are best practices.
I wrote about the importance of extruder barrel alignment and how it should be done several years ago, but aligning the extruder barrel is not the whole solution. The downstream equipment must also be aligned and supported properly to maintain the properly aligned barrel.
After breaking a screw, a client of mine brought in a competent company to align the barrel. But the new screw lasted all of three weeks. Upon startup one day, the screw broke, and in the process also heavily damaged the barrel, requiring its replacement as well.
I was asked to be there for the startup with the new barrel and screw. The extruder was started and I immediately heard a grinding sound and noticed a large fluctuation of the drive amps. I had the extruder shut down immediately and asked how they had lined up the downstream components to the extruder.
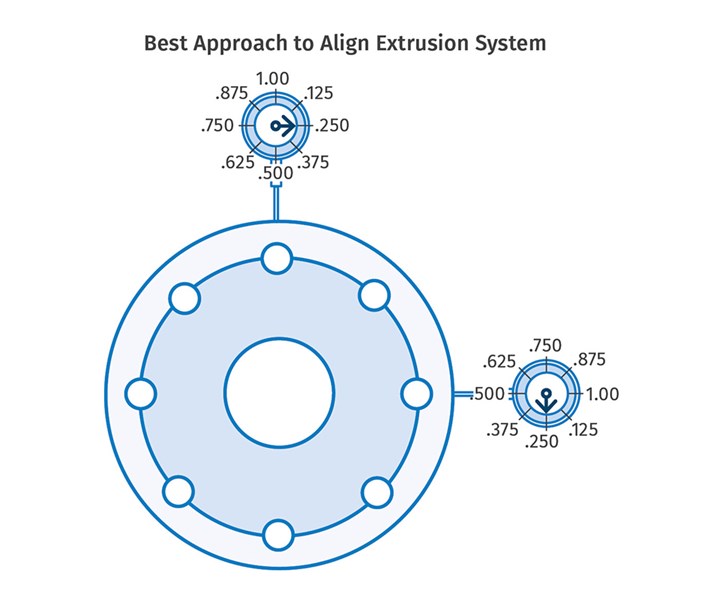
The best approach is to complete the barrel alignment using optical- or laser-alignment equipment. Also put dial indicators, as shown here, anchored to an independent support to maintain that alignment as the downstream equipment is attached and heated up.
The screen changer was a double-piston type and weighed about 4000 lb. Although it was supported in a stand on rubber casters, the floor was very uneven, and the installers had simply pushed the flanges close together and then used the bolts to pull the screen changer into its position on the barrel with no regard for its effect on the barrel alignment.
Next was the melt pump, which weighed about 1750 lb without the drive motor and reducer. Again, the unit was on a stand with rubber casters, but the installers had once more made no effort to align it. Instead, they simply pulled it into place against the screen changer and used the bolts to draw it into position. Finally the die was coupled to the melt pump with the same procedure on a similar stand.
I instrumented the extruder barrel flange with two dial indicators mounted at 90° to one another, as shown in the accompanying illustration. As the screen changer was loosened from the barrel, the vertical dial indicator showed a rise in the barrel of 0.255 in. and the horizontal indicator showed a lateral movement of slightly over 0.100 in.
Barrel alignment is not just a matter of lining up the barrel itself but maintaining that alignment after the whole system is assembled.
Obviously that totally destroyed the alignment of the barrel to the drive quill, and the resultant bending and repositioning of the barrel caused severe contact between the screw and the barrel bore. The point here is that barrel alignment is not just a matter of lining up the barrel itself but maintaining that alignment after the whole system is assembled.
The best approach is to complete the barrel alignment using optical- or laser-alignment equipment, then put dial indicators anchored to an independent support to maintain that alignment as the downstream equipment is attached and heated up. Not only will the mechanical attachment of downstream equipment affect the alignment, but the heating-up phase is also important, as the downstream components and the barrel itself can change position substantially as thermal expansion affects the entire assembly. The only way to determine if the alignment is being altered when completing assembly of the line is to instrument the barrel flange.
The only way to determine if the alignment is being altered when completing assembly of the line is to instrument the barrel flange.
This is a very simple procedure and should be used every time the downstream equipment is reinstalled on the barrel, even if the downstream equipment is mounted on steel rails. The longer the barrel and the heavier the downstream equipment, the more care should be exercised in reassembly of the line. In the case noted, it would have saved two screws and barrels, along with the associated downtime. Estimated total cost was in the hundreds of thousands of dollars.
About the Author: Jim Frankland is a mechanical engineer who has been involved in all types of extrusion processing for more than 40 years. He is now president of Frankland Plastics Consulting, LLC. Contact jim.frankland@comcast.net or (724) 651-9196.
Related Content
The Importance of Barrel Heat and Melt Temperature
Barrel temperature may impact melting in the case of very small extruders running very slowly. Otherwise, melting is mainly the result of shear heating of the polymer.
Read MoreShredding Thin Film: How to Do It Right
While many processors recoil at this task, a little know-how in shredding equipment, processing, and maintenance should add the necessary confidence.
Read MoreHow to Select the Right Tooling for Pipe Extrusion
In pipe extrusion, selecting or building a complementary set of tooling often poses challenges due to a range of qualitative factors. Here’s some guidance to help you out.
Read MoreWhy Are There No 'Universal' Screws for All Polymers?
There’s a simple answer: Because all plastics are not the same.
Read MoreRead Next
For PLASTICS' CEO Seaholm, NPE to Shine Light on Sustainability Successes
With advocacy, communication and sustainability as three main pillars, Seaholm leads a trade association to NPE that ‘is more active today than we have ever been.’
Read MoreBeyond Prototypes: 8 Ways the Plastics Industry Is Using 3D Printing
Plastics processors are finding applications for 3D printing around the plant and across the supply chain. Here are 8 examples to look for at NPE2024.
Read More