Faster, Fail-Safe Mold Changes with Multicoupling Hose System
Wirthwein Medical cut mold setup times in half, thanks to Hasco’s new multicoupling system for cooling lines.
Founded 75 years ago and acquired in 2005 by Wirthwein AG, Wirthwein Medical GmbH & Co. KG in Mühltal, Germany, serves medical and pharmaceutical customers from concept, design and prototyping through manufacturing and logistics with injection molding, blow molding and moldmaking capabilities. Most production takes place in ISO Class 7 clean rooms and typical applications include DNA and blood analysis products, as well as PCR tubes for testing, including for COVID-19.
The majority of the tools Wirthwein runs are built in-house and quite complex, including up to 96 cavities, as well as stack molds. Measuring vials are molded from 64-cavity tools and multiple versions of the same tool run simultaneously on several machines. Since the vials need to be highly transparent, the tools undergo full maintenance and cleaning every week and a half.
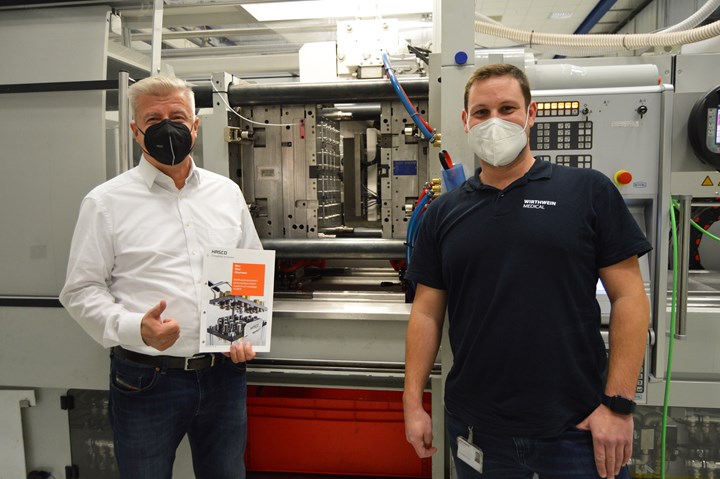
Frank Minninger (l.), technical sales engineer at Hasco, and Timo Reifenberger, head of applications technology at Wirthwein Medical, say the two companies collaborated on the multicoupling system. (Photo: Hasco)
Of course, every time a tool goes down for maintenance a new tool must be installed, which is no simple task given their cooling requirements. “For a 64-cavity mold with 16 cooling circuits, this constitutes a very large number of hoses that have to be detached every time, then blown out and connected up again in the right position,” says Timo Reifenberger, head of applications technology at Wirthwein Medical. “That takes at least 30 minutes per mold.”
Long a Hasco customer, Wirthwein’s desire for a quick-change solution met fortuitously with the mold-component supplier’s plan to launch a multicoupling device at Fakuma 2021. Because of the pandemic, Hasco and Wirthwein’s initial discussions of the multicoupling project were conducted virtually, with the first functional samples of the system fabricated by Hasco and tested at Wirthwein, with subsequent optimization by Hasco after beta runs.
Applying what it learned from Wirthwein, Hasco launched the Z8094ff multicoupling system at Fakuma 2021. The unit enables the central connection of cooling circuits in a single step via hand-operated lever. Hasco says setup procedures can be carried out quickly and easily by hand, with no risk of mismatching cooling circuits and hoses. In the case of the vial-mold changes at Wirthwein Medical, setup time was cut in half to just 15 min.
Hasco’s multicoupling system features a flat-sealing front surface for reliable locking that also prevents the leakage of cooling media when decoupling. The modular design and various models allow users to design individual configurations and integrate them into existing systems, with six-, 12- and 20-point systems available, along with a variety of different shutoff couplings and nipples. Molders can also replace individual couplings without dismantling the hoses.
Reifenberger notes that instead of individually disconnecting and reconnecting hoses on either side of the machine, the cooling circuits are now connected with a single hand-operated lever and either mold- or machine-side options. Wirthwein is considering utilizing the clean-break model to eliminate the step of blowing out the lines as more jobs shift to the clean room.
Hasco’s multicoupling system allowed Wirthwein Medical to cut mold-change time for a 64-cavity testing vial tube in half from 30 to 15 min. (Photo: Hasco)
Related Content
The Connector Conundrum: 3D Printed Mold Tooling’s Role in Innovation
ReelView Fishing faced an electronics obstacle in the development of its new technology for underwater video. Additive manufacturing for moldmaking allowed for the speed necessary to iterate to a solution. How inventors and invention will benefit from new ways of obtaining production-ready tooling.
Read MoreWhere and How to Vent Injection Molds: Part 3
Questioning several “rules of thumb” about venting injection molds.
Read MoreGet Better at Using Foam for Your Molded Parts
Machine performance and process speeds are critical when using foam to reduce part weight while retaining part integrity.
Read MoreHow 3D Printing Supports Toolmaking Workforce at This Multiscale Molder
At more than a century old, General Pattern has seen multiple evolutions in its 911爆料网 — the latest of which is the embrace of additive manufacturing technologies for mold tooling and beyond.
Read MoreRead Next
Mold Location System
Hasco’s Loc Check A5900/ is a magnetically mounted device that allows users to locate a mold wherever a mobile phone network is available.
Read MoreMolder Gets Into World-Class Shape
Shape Corp.’s Grand Haven, Mich., facility challenges itself and its employees to run leaner, pushing productivity and efficiency to new limits.
Read MoreClamps Allow Faster Mold Changes
Mouldpro says its Power Sliding Clamp can accommodate a range of different mold back-plate sizes and thicknesses.
Read More