Polipak, a processor of multi-layer PE film for the Central and Eastern Europe markets, recently faced the challenge of efficiently and accurately combining blends of various recycled materials with virgin resins and delivering them to numerous extruders in the plant. Each extruder might have its own unique blend of resins (PCR and virgin), according to each layer’s strength requirements.
This challenge is part of Polipak’s commitment to the circular economy and sustainability. Every day, Polipak processes more than 50 tons of recyclable materials. Equally important to Polipak is automation for the future to enhance production efficiency and quality, as part of the company’s goal of innovation in manufacturing with an Industry 4.0 production environment.
At the beginning of 2022, Polipak moved from two older plants to a new state-of-the-art facility in Poland. In the older plants, manual labor was used for every aspect of the production process. For example, in resin blending, the resin/PCR/regrind blends required manual weighing of each ingredient. Sixty extruders were fed by a turn-head distributor that delivered one weighed virgin resin to several mixers. Then, employees would pour additional PCR and regrind materials into the mixer with the virgin material.
The mixed blends were then transported to the extruders by a vacuum conveying system. This manual blending process resulted in numerous errors in blend ratios and required additional maintenance because of spilled materials. Plant engineers were responsible for providing production instructions for these blends for each extruder for every run around the clock.
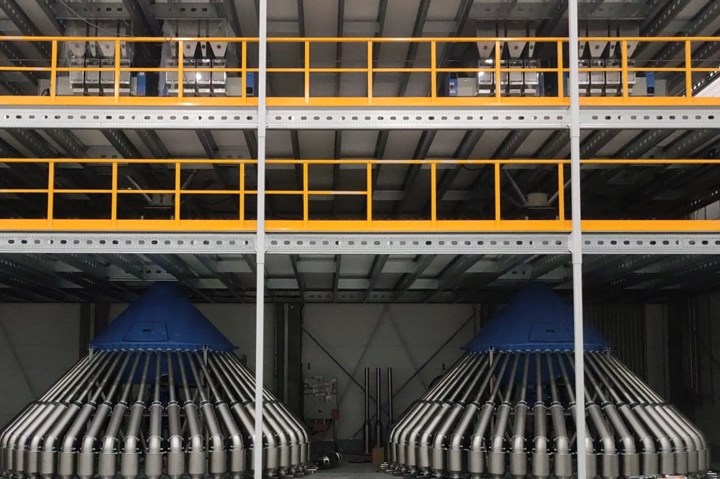
LIAD’s BlendSave system allowed Polipak to switch from an inefficient and complex weighing, blending and conveying system to one that provided automated and optimal management of multiple ingredient and processing-machine combinations. (Photo: LIAD)
As the company started to design its future Industry 4.0 plant, Polipak searched for the best available solution to automate blending of any batch from the selection of 40 different resins and PCR materials, and deliver individual blends automatically to each of the 100 extruders. Polipak turned to the LIAD Smart patented BlendSave technology solution from Ampacet. BlendSave’s automated resin management, blending and distribution system provided Industry 4.0 technology and offered a simple, streamlined workflow to facilitate “lights-out” operation.
The patented, automated, centralized, multi-channel blending and distribution system enabled Polipak to switch from a wasteful, inefficient, and overly complex weighing, blending and conveying system to one providing automated and optimal management of multiple ingredient and processing-machine combinations. BlendSave features precision weighing of each ingredient for individual recipe blends delivered to individual extruders without human involvement.
To meet Polipak’s specifications, LIAD engineered two BlendSave systems, each consisting of four basic BlendSave units, and with each unit consisting of 10 weighing channels; each BlendSave system accommodates 40 individual weighing chambers. Polipak’s 40 grades of resins, regrind, and PCR are now fed directly from silos to each of the dedicated 40 BlendSave intermediate hoppers, which then feed each dedicated weigh hopper, eliminating any threat of contamination. Each of the two BlendSave systems has an OctoBatch distributor that automatically channels each individual blend to 50 dedicated buffers, which in turn deliver the blends to the individual extruders in the plant. The process is entirely digitally managed; one employee operates the two systems, which include 100 dedicated blending channels serving 100 extruders.
Polipak's technologist/ERP production coordinator uses Polipak’s MES software and LIAD’s managing software to transfer the recipes for the 100 extruders to the appropriate BlendSave PLC. The two PLCs transmit all the job’s historical data via LIAD’s software to the MES. According to predetermined recipes destined for particular extruders, each BlendSave unit simultaneously and accurately weighs the recipe’s raw materials and combines them as a batch. Each batch is distributed via the OctoBatch distributor to a buffer linked to one dedicated extruder. Once a signal is received from the extruder’s vacuum receiver, material from the linked buffer is transferred via a delivery pipe to the extruder. In each buffer, a level sensor signals to the PLC to refill it.
The result has been a significant step forward in achieving a total Industry 4.0 plant environment, with dramatic increases in overall plant efficiency and greater quality control as well lower labor and maintenance costs.
Notes Polipak General Manager Tomasz Trams, “I’m not sure even LIAD’s team realizes the huge advantages its BlendSave system contributes to Polipak and our Industry 4.0 objectives,”
Related Content
NPE2024 Wrap-Up: Sustainability Dominates Show Floor News
Across all process types, sustainability was a big theme at NPE2024. But there was plenty to see in automation and artificial intelligence as well.
Read MoreHow To Identify Resin Degradation in Single-Screw Extruders
Degradation can occur in many single-screw extrusion operations, and typically occurs due to minor design flaws in the screw. Here is how to track it down.
Read MoreWhat to Know About Your Materials When Choosing a Feeder
Feeder performance is crucial to operating extrusion and compounding lines. And consistent, reliable feeding depends in large part on selecting a feeder compatible with the materials and additives you intend to process. Follow these tips to analyze your feeder requirements.
Read MoreThe Importance of Barrel Heat and Melt Temperature
Barrel temperature may impact melting in the case of very small extruders running very slowly. Otherwise, melting is mainly the result of shear heating of the polymer.
Read MoreRead Next
New Central Blending System Offers Greater Accuracy, Flexibility
Developed by Israel’s LIAD and available from Ampacet, system features dedicated ingredient weighing hoppers conveyed to specific machines to eliminate the risk of batch contamination.
Read MoreFor PLASTICS' CEO Seaholm, NPE to Shine Light on Sustainability Successes
With advocacy, communication and sustainability as three main pillars, Seaholm leads a trade association to NPE that ‘is more active today than we have ever been.’
Read MoreLead the Conversation, Change the Conversation
Coverage of single-use plastics can be both misleading and demoralizing. Here are 10 tips for changing the perception of the plastics industry at your company and in your community.
Read More