Micro Mirrors Make for Special Molded Effects
Originally invented for use in currency, a new, patented optical security technology allows anti-counterfeiting design effects to be incorporated directly into injection-molded products and packaging.
Lumenco Inc., a pioneer in micro-optics applied in anticounterfeiting and other fields, announced that its subsidiary Nanopixel has introduced MicroEdge—a patented optical security feature that can be molded directly into the surface of plastic products or packaging.
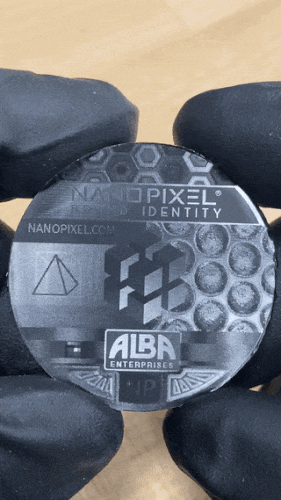
The visual effects MicroEdge creates are based upon “voxels” or points of light in three dimensional space either above or below the focal point.
Photo Credit: Alba Enterprises
MicroEdge features can include a combination of three-dimensional, animated, flip, or on-off images, which unlike traditional holography, are viewable under ordinary diffused lighting conditions. MicroEdge inventor and Lumenco/Nanopixel CEO, Mark Raymond told Plastics Technology that MicroEdge was originally created for the banknote industry. Taking years of development and millions of dollars in R&D investments, MicroEdge eventually evolved into a “micro-mirror” technology named Dycyfer, which could be applied in currency, tax stamps and brand protection. “We invented MicroEdge as a challenge from Bank of Canada for coins,” Raymond said, “but it only has been used in prototyping for that technology.”
Points of Light
The visual effects MicroEdge creates are based upon “voxels” or points of light in three dimensional space either above or below the focal point. “What the viewer sees in not a ‘reflection’ per se,” Raymond explains, “it is a pixel created by at least 20 micro mirrors.” Each pixel, in turn, is actually a point of light at the intersection of the vector of the mirrors. The sizes of the micro mirrors in the mold are usually between 20 and 50 microns, but can be more than 1000 microns. “This selection is based upon the polymers and the overall design of the piece,” Raymond said.
Raymond says a key difference between MicroEdge and conventional holography, is that it can be scaled with different sized mirrors or facets to create the voxels. Also, unlike holography, MicroEdge’s effects work in all lighting conditions. “These types of structures can be created in the injection molding process accurately, and are more robust and won’t be filled with soil or oil from someone’s hands,” Raymond said. A refractive rather than a reflective technology, MicroEdge is based upon the index of refraction of clear materials to manage light.
To design the network of micromirrors, MicroEdge applies a proprietary software. “Keep in mind that for MicroEdge, even a small image uses hundreds of thousands of micro mirrors—or millions—all with theoretically different vectors or directional cosines,” Raymond says.
Assist from Alba
Technical assistance during production testing and development of MicroEdge was provided by Alba Enterprises. Alba, which acts as a distributor of the Babyplast micro injection molding machines, among other products, utilized a Babyplast machine to trial the technology. Rich Oles, president of Alba Enterprises, said his company also helped source tooling for product. The tool’s first shots achieved feature definition of 60% to 65%, with subsequent efforts getting 80% to 85% feature definition. “We have other technologies to get to the 100% mark,” Oles said.
Nanopixel said in a realease that it is “in dialogue with product marketers and designers to bring MicroEdge features to product shelves by Q3 2022.”
Related Content
Understanding the Effect of Pressure Losses on Injection Molded Parts
The compressibility of plastics as a class of materials means the pressure punched into the machine control and the pressure the melt experiences at the end of fill within the mold will be very different. What does this difference mean for process consistency and part quality?
Read MoreUsing Data to Pinpoint Cosmetic Defect Causes in Injection Molded Parts
Taking a step back and identifying the root cause of a cosmetic flaw can help molders focus on what corrective actions need to be taken.
Read MoreIs There a More Accurate Means to Calculate Tonnage?
Molders have long used the projected area of the parts and runner to guesstimate how much tonnage is required to mold a part without flash, but there’s a more precise methodology.
Read MoreUse These 7 Parameters to Unravel the Melt Temperature Mystery
Despite its integral role in a stable process and consistent parts, true melt temperature in injection molding can be an enigma. Learning more about these seven parameters may help you solve the puzzle.
Read MoreRead Next
See Recyclers Close the Loop on Trade Show Production Scrap at NPE2024
A collaboration between show organizer PLASTICS, recycler CPR and size reduction experts WEIMA and Conair recovered and recycled all production scrap at NPE2024.
Read MoreLead the Conversation, Change the Conversation
Coverage of single-use plastics can be both misleading and demoralizing. Here are 10 tips for changing the perception of the plastics industry at your company and in your community.
Read MorePeople 4.0 – How to Get Buy-In from Your Staff for Industry 4.0 Systems
Implementing a production monitoring system as the foundation of a ‘smart factory’ is about integrating people with new technology as much as it is about integrating machines and computers. Here are tips from a company that has gone through the process.
Read More