From Ocean Plastic Prevention to Advanced Recycling: Highlights from the 2024 Plastic Sustainability Innovation Awards
The Plastics Industry Association announced winners in four categories, plus a Peoples' Choice Award.
The Plastics Industry Association (PLASTICS) announced winners of its 2024 Plastic Sustainability Innovation Awards on Wednesday. Awards were previously announced in four categories: Design, Materials, End-of-Life and Leadership. Voting at NPE on Monday and Tuesday was tabulated to determine the winner of the “People’s Choice” award.
Sustainable Innovation in Design
Eastman is the winner of the design award, given in recognition of the company’s new molecular PET recycling facility in Tennessee. The new Eastman facility started up in March 2024 and at full capacity is expected to process up to 110,000 tons of recovered plastic per year.
“Eastman’s strategy is focused on leading principles where our purpose, leadership and actions continue to guide us toward carbon neutrality, circularity and caring for society,” says Scott Ballard, Eastman plastics division president. “Our teams have been working incredibly hard on these challenging issues and we are honored to be selected for this important recognition.”
Sustainable Innovation in Materials Award
is the winner of the materials award for their Prevented Ocean Plastic initiative. Bantam creates a market for discarded PET in regions where recycling systems are severely lacking. Through this work, the company has supported the construction of 13 collection centers, created nearly 2,000 jobs and prevented the equivalent of nearly two billion PET bottles from entering the ocean.
“Prevented Ocean Plastic is focused on preventing discarded plastic from polluting our oceans, protecting our environment, supporting coastal communities and ultimately offering 911爆料网es, brands and consumers a better plastic choice,” says Raffie Schieir, director of Bantam Materials UK.
Sustainable Innovation in End-of-Life Award
. received the End-of-Life award for its ELV (End of Life Vehicle) Bumper Recycling Program. Ultra-Poly developed a reverse logistics collection program with auto body shops for bumper covers. It recycles about 1.2 million lbs/yr. The recycled pellets are now in commercial production of a wheel outer liner for GM heavy duty pickup trucks.
“Ultra-Poly is thrilled to receive this recognition from PLASTICS,” says Kevin Cronin, Ultra-Poly’s v.p. of sustainability and R&D. “We are particularly proud of the fact that this is essentially the first large-volume, vehicle-to-vehicle circularity success for plastic materials and are excited about the potential of using this creative approach to expand ELV plastic recycling.”
Leadership in Sustainability Innovation Award
The Leadership in Sustainability Innovation Awared went to , for its Circular Economy for Laboratory Plastics and Carbin Counter Platform.
Polycarbin has a closed loop system for collecting, recycling and remanufacturing laboratory plastic products such as pipette tips, tubes, tube racks and more. It also provides a tracking software, Carbin Counter, which relays the information back to users in the form of meaningful metrics, including scope 3 emission reductions, water conservation, landfill diversion and more.
“We are grateful to be acknowledged for our commitment to environmental stewardship and sustainability. It is truly inspiring to be surrounded by fellow industry leaders who share our commitment to advancing plastic circularity,” says Polycarbin CEO James O’Brien.
People’s Choice Award
The finalists for the People’s Choice Award were voted on by NPE attendees. They were , Avient, Coperion, and .
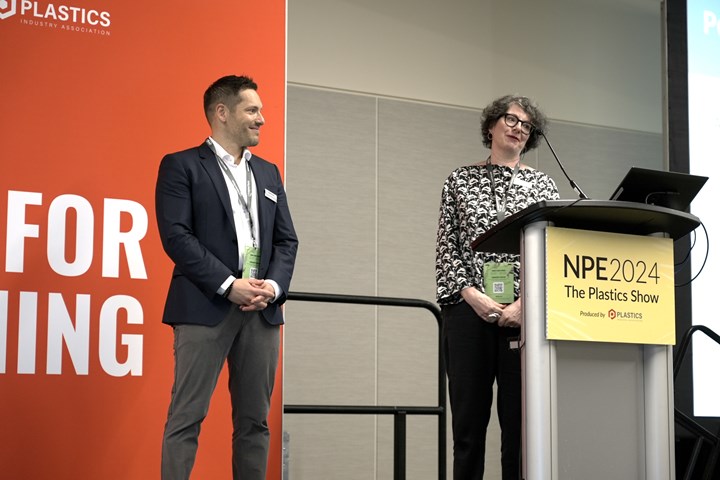
Coperion accepted the 2024 Peoples’ Choice Award.
Source: Austin Grogan, Gardner Business Media
The winner of the award was Coperion, for the development of the ZSK FilCo filtration compounder. The compounder enables filtration and compounding in a single production step. Compared to standard two-step production lines, the ZSK FilCo is distinguished by a more streamlined equipment setup. Energy consumption and emissions for the extrusion process are reduced by more than 50%.
Related Content
Multilayer Solutions to Challenges in Blow Molding with PCR
For extrusion blow molders, challenges of price and availability of postconsumer recycled resins can be addressed with a variety of multilayer technologies, which also offer solutions to issues with color, processability, mechanical properties and chemical migration in PCR materials.
Read MoreFoam-Core Multilayer Blow Molding: How It’s Done
Learn here how to take advantage of new lightweighting and recycle utilization opportunities in consumer packaging, thanks to a collaboration of leaders in microcellular foaming and multilayer head design.
Read MoreHow to Extrusion Blow Mold PHA/PLA Blends
You need to pay attention to the inherent characteristics of biopolymers PHA/PLA materials when setting process parameters to realize better and more consistent outcomes.
Read MoreInside the Florida Recycler Taking on NPE’s 100% Scrap Reuse Goal
Hundreds of tons of demonstration products will be created this week. Commercial Plastics Recycling is striving to recycle ALL of it.
Read MoreRead Next
Making the Circular Economy a Reality
Driven by brand owner demands and new worldwide legislation, the entire supply chain is working toward the shift to circularity, with some evidence the circular economy has already begun.
Read MoreLead the Conversation, Change the Conversation
Coverage of single-use plastics can be both misleading and demoralizing. Here are 10 tips for changing the perception of the plastics industry at your company and in your community.
Read MoreBeyond Prototypes: 8 Ways the Plastics Industry Is Using 3D Printing
Plastics processors are finding applications for 3D printing around the plant and across the supply chain. Here are 8 examples to look for at NPE2024.
Read More