Finnish Startup Gets IMSE Lighting Patent
TactoTek’s newly-patented technology available for licensing.
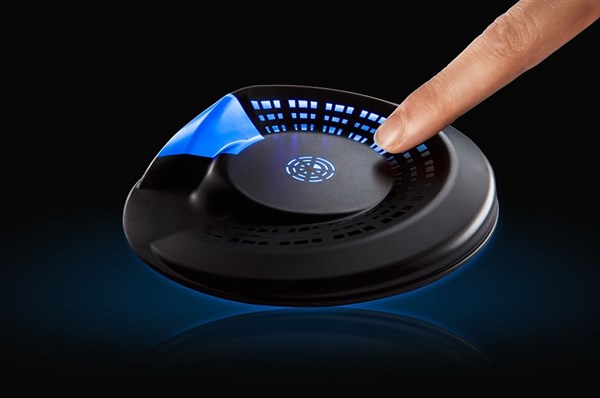
TactoTek’s newly-patented technology available for licensing.
An interesting technology from a Finnish startup that has a unique method for integrating printed electronics such as circuitry, touch controls and antennas, as well as discrete electronic components such as LEDs, into injection molded plastics has been issued a U.S. patent (9297675). Applications for the so-called “illuminated indicator structures for electronic devices” include automotive, home appliances, wearables and health care.
The new technology from TactoTek, based in Oulu, Finland (U.S. office in Cupertino, Calif.) reportedly enables sophisticated lighting in very thin 3D plastic ‘smart surfaces’. “This patent recognizes a key innovation for injection molded structural electronics (IMSE) technology—employing the plastic material that is the structure of a part as a light guide. Using this technique, we can create very bright, evenly distributed illumination within structures as thin as 2-millimeters (0.079 in.),” according to CTO and co-founder Antti Keranen.
For illumination, TactoTek’s IMSE technology consolidates printed electronics and LEDs within the 3D molded plastic part and uses the plastics themselves to conduct light. This, in contrast with traditional electronics designs, which typically include a cosmetic surface structure and use a separate light pipe structure to direct lighting to the surface from a flat, rigid printed circuit board (PCB).
TactoTek’s approach of using the molded cosmetic surface as a light guide removes design constraints that had previously prescribed thick, multi-part assemblies, explains head of product management Hasse Sinivaara. “As we remove parts, we remove design time, weight and minimize electrical and mechanical assembly—very appealing when considering form factor innovation and total cost of ownership.”
TactoTek’s patented and patent-pending technologies integrate a mixture of well-known production technologies into a unique approach that enables mass production of 3D structural electronics. These include flexible circuit printing, surface-mounting electronic components, thermoforming, in-mold labeling (IML), and injection molding.
The approach starts with an IML material. Decoration, if desired, is printed, followed by conductive circuitry, and in some designs, printed touch controls and printed antennas. Electronic components are mounted using standard high-speed pick-and-place machinery. Electronics can be as simple as LEDs or as complex as microprocessors and are affixed to the IML using specialized adhesives able to withstand the temperature and pressure of injection molding. With electronics in place, the IML carrier is used as an insert for injection molding.
According to senior v.p. of marketing Dave Rice, the company uses a range of plastics that are standard for high-pressure, high-temperature injection molding, including: PC, ABS, and acrylic for rigid structures; TPU and hybrids, e.g., TPU/silicone for flexible structures.
Here is Rice’s answer when I asked if the company plans to license its newly-patented technology: “Our core 911爆料网 model is to help customers adapt their traditional electronics designs to TaktoTek IMSE technology and, develop mass production ready prototypes. For mass production, in some cases, we will manufacture parts ourselves; in most cases, we will license our technology and train a third party—typically an established Tier 1 supplier, to mass produce those parts.”
Related Content
Polymer Showdown — PPO vs. PA66: May the Best Material Win
Second in a series, an expert from plastics engineering consultancy The Madison Group pits leading thermoplastics against each other to see how they differ in processing characteristics, chemical resistance, thermal and mechanical performance, and more.
Read MoreScaling Up Sustainable Solutions for Fiber Reinforced Composite Materials
Oak Ridge National Laboratory's Sustainable Manufacturing Technologies Group helps industrial partners tackle the sustainability challenges presented by fiber-reinforced composite materials.
Read MorePrices Up for All Volume Resins
First quarter was ending up with upward pricing, primarily due to higher feedstock costs and not supply/demand fundamentals.
Read MoreThe Fantasy and Reality of Raw Material Shelf Life: Part 1
Is a two-year-old hygroscopic resin kept in its original packaging still useful? Let’s try to answer that question and clear up some misconceptions.
Read MoreRead Next
Beyond Prototypes: 8 Ways the Plastics Industry Is Using 3D Printing
Plastics processors are finding applications for 3D printing around the plant and across the supply chain. Here are 8 examples to look for at NPE2024.
Read MoreLead the Conversation, Change the Conversation
Coverage of single-use plastics can be both misleading and demoralizing. Here are 10 tips for changing the perception of the plastics industry at your company and in your community.
Read More