Japanese Automaker Joins Stratasys to 3D Print Custom Parts
More stories are emerging that take 3D printing beyond just the prototyping phase to factory tooling and even short-run production, exploiting the technology for mass customization of consumer products.
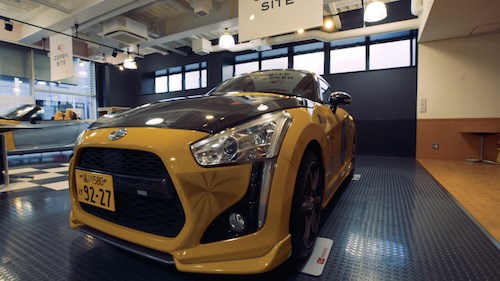
More stories are emerging that take 3D printing beyond just the prototyping phase to factory tooling and even short-run production, exploiting the technology for mass customization of consumer products.
Japanese automaker Daihatsu Motor Co., Ltd, (Daihatsu) is one of the first manufacturers to deliver on the 3D printing vision of mass customization of end-use parts, collaborating with Stratasys and top local designers. The company was looking to expand the market for customized plastic bodied cars and saw 3D-printing technology as an effective means to this goal.
Based in Ikeda, Osaka, Japan, Daihatsu partnered with 3D printing company , Kota Nezu from industrial design company and 3D creator Sun Junjie to turn the vision into reality. Designers created 15 "Effect Skins"—intricate geometric and organic patterns in 10 different colors that are 3D printed using Stratasys’ Fortus 3D printers. The skins may be ordered for front and rear bumpers and fenders.
Here’s a video showcasing the customized car design with 3D printing.
The Effect Skins are 3D-printed on Fortus Production 3D Printers from Stratasys using ASA thermoplastic. "What would have taken two to three months to develop can now be produced in two weeks," said Osamu Fujishita, general manager, corporate planning department, brand DNA office, Daihatsu Motor Co.
This Effect Skins project illustrates how 3D printing can create on-demand product parts with high customizability and rich design properties. In fact, according to Kota Nezu of Zung Design: "This project would not have been possible with traditional manufacturing or tooling methods.”
"We believe on-demand production with 3D printing offers definite benefits to supply chain efficiencies," said Osamu Fujishita. "And it allows easy access for customers."
The Effect Skin project is being tested in 2016 in select markets with plans for commercialization in early 2017.
Related Content
-
Get Color Changes Right In Extrusion Blow Molding
Follow these best practices to minimize loss of time, material and labor during color changes in molding containers from bottles to jerrycans. The authors explore what this means for each step of the process, from raw-material infeed to handling and reprocessing tails and trim.
-
Multilayer Solutions to Challenges in Blow Molding with PCR
For extrusion blow molders, challenges of price and availability of postconsumer recycled resins can be addressed with a variety of multilayer technologies, which also offer solutions to issues with color, processability, mechanical properties and chemical migration in PCR materials.
-
3D Printed Spine Implants Made From PEEK Now in Production
Medical device manufacturer Curiteva is producing two families of spinal implants using a proprietary process for 3D printing porous polyether ether ketone (PEEK).