LLDPE Replaces Paper In Additive Packaging
The new packaging system replaces paper bags with more robust LLDPE bags.
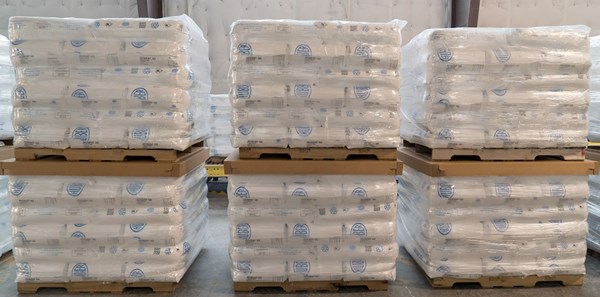
The new packaging system replaces paper bags with more robust LLDPE bags.
Among the many times through the years that I have reported on plastic chemicals and additives news, I’d say it’s been less than a handful of times where the topic was about their packaging. Typically, it’s about new and/or improved versions of additives that improve performance of plastics and/or their physical form (e.g., pellets, beads) which allow for easier handling. Some small particle additives, in particular, have traditionally posed particular challenges.
So, I found it interesting to hear that J.M. Huber Corp.’s Huber Engineered Materials division had invested in an innovative, multi-million dollar packaging system, which replaces paper bags with a conversion to more robust LLDPE bags at its precipitated amorphous silica Havre de Grace, Md., production facility. Huber’s silicas and silicates are used in a variety of industries and when targeted as an anti-blocking agent for plastics, polyolefins is a key application.
A Huber spokesman explained that the new filling technology and use of LLDPE bags for small particle materials such as silicon dioxide is just emerging. “Use of plastic bags is more and more common for gardening items and masonry materials….those industries have been converting for many years but are much easier to package than silica because of the large particle sizes and high bulk density. The expertise in the design of the packaging equipment, coupled with the emerging technology in the design of the films used to create the LLDPE bags effectively adapts to handling silica’s unique properties,” he says.
Asked if the LLDPE choice is unusual for packaging these type of additives, the Huber source notes that PP is most commonly used in both Asia, where sacks are reused for other purposes, and India, due to lack of trees/paper. He notes, however, that these PP bags release considerably more dust and are manually filled. Here’s more on Huber’s system and bags:
• Huber’s new packaging platform is being introduced systematically across the globe with automatic filling equipment already in place in select production facilities in the European and American regions, with the intention to do the same in Asia in 2017. (The company is a global leader in precipitated silica with seven manufacturing sites strategically located across North America, Europe, and Asia.)
• The improved LLDPE bags offer stronger tensile strength.
• The LLDPE bags minimize the nuisance of dust.
• They eliminate trapped air within each LLDPE bags, making the packages more easily stackable for more stable pallets during shipment, unloading, and warehousing.
• The LLDPE bags also provide increased printing and labeling options.
• The new packaging is also easily recyclable which is integral to Huber’s commitment to sustainability.
According to the Huber spokesman, the novel packaging’s development was also influenced by customers’ requests for improved performance over paper bags—which are susceptible to moisture, excessive dusting, improved recycling needs, emerging food safety, and employee health exposure regulations.
For more on Huber and additives offered, see PT’s additives database.
Related Content
How Polymer Melts in Single-Screw Extruders
Understanding how polymer melts in a single-screw extruder could help you optimize your screw design to eliminate defect-causing solid polymer fragments.
Read MoreSingle vs. Twin-Screw Extruders: Why Mixing is Different
There have been many attempts to provide twin-screw-like mixing in singles, but except at very limited outputs none have been adequate. The odds of future success are long due to the inherent differences in the equipment types.
Read MoreWhat to Know About Your Materials When Choosing a Feeder
Feeder performance is crucial to operating extrusion and compounding lines. And consistent, reliable feeding depends in large part on selecting a feeder compatible with the materials and additives you intend to process. Follow these tips to analyze your feeder requirements.
Read MorePart 2 Medical Tubing: Use Simulation to Troubleshoot, Optimize Processing & Dies
Simulation can determine whether a die has regions of low shear rate and shear stress on the metal surface where the polymer would ultimately degrade, and can help processors design dies better suited for their projects.
Read MoreRead Next
People 4.0 – How to Get Buy-In from Your Staff for Industry 4.0 Systems
Implementing a production monitoring system as the foundation of a ‘smart factory’ is about integrating people with new technology as much as it is about integrating machines and computers. Here are tips from a company that has gone through the process.
Read MoreLead the Conversation, Change the Conversation
Coverage of single-use plastics can be both misleading and demoralizing. Here are 10 tips for changing the perception of the plastics industry at your company and in your community.
Read MoreBeyond Prototypes: 8 Ways the Plastics Industry Is Using 3D Printing
Plastics processors are finding applications for 3D printing around the plant and across the supply chain. Here are 8 examples to look for at NPE2024.
Read More