Reifenhauser Converts Lab Lines to Produce Face Masks
Will operate four-shift operation 24/7 till further notice. Says it will produce enough material to make 1 million face masks a day.
Reifenhauser has converted two of its R&D lines at its nonwovens technology center in Troisdorf, Germany to full-production system for making meltblown material for face masks.
In a press released issued by the company, it said the two meltblown lines will be operated in four-shift operation 24/7, which it says will produce enough PP material to make 1 million face masks a day. Trial operations will be almost completely suspended during this period. Said Michael Maas, who is responsible for the Reifenhauser nonwoven test plant: “Due to the corona pandemic, the customer visits and tests that were actually planned have increasingly been cancelled, so that plant capacities and personnel capacities have been freed up anyway. Switching the plant from test to production operation therefore makes double sense.”
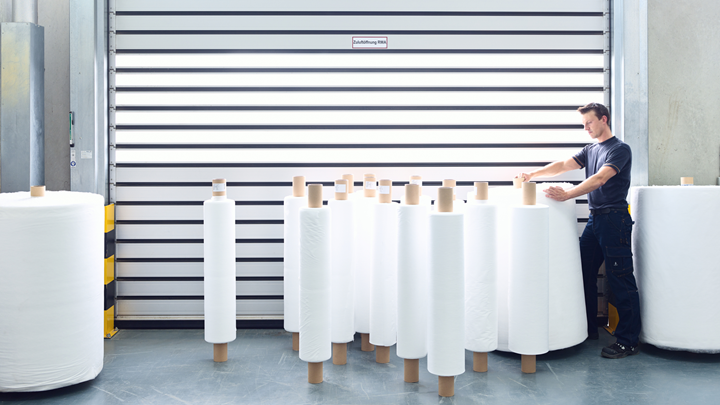
The meltblown material from the nonwoven technology center is already
sold out for the next five weeks. However, Reifenhäuser says it continues
to look for opportunities to strengthen the local supply during this crisis.
The company is in close contact with associations, authorities and other
companies, according to the release.
Added Dr. Bernd Kunze, CEO of Reifenhäuser Reicofil: “We have considered what contribution we can make in this crisis. This is of course mainly the fast delivery of meltblown lines to build up additional capacities. We have drastically reduced our delivery times here. But we also wanted to provide support at shorter notice. Until the currently lacking capacities are built up, we are therefore stepping in with the test plants in our pilot plant station. Not using this capacity now would be irresponsible in our view.”

Related Content
-
New Blown-Film Cooling Technologies Set to Debut at NPE2024
Cooling specialist Addex to roll out new auto-profiling air ring for rotating dies, and new single-plenum air ring.
-
Flexible-Film Processor Optimizes All-PE Food Packaging
Tobe Packaging’s breakthrough was to create its Ecolefin PE multilayer film that could be applied with a specialized barrier coating.
-
How to Effectively Reduce Costs with Smart Auxiliaries Technology
As drying, blending and conveying technologies grow more sophisticated, they offer processors great opportunities to reduce cost through better energy efficiency, smaller equipment footprints, reduced scrap and quicker changeovers. Increased throughput and better utilization of primary processing equipment and manpower are the results.