The ‘Three Rs' of Sustainability: Are They All Equal in Priority?
Reduce, Reuse, Recycle—Which of these is most accessible to more manufacturers in the near term?
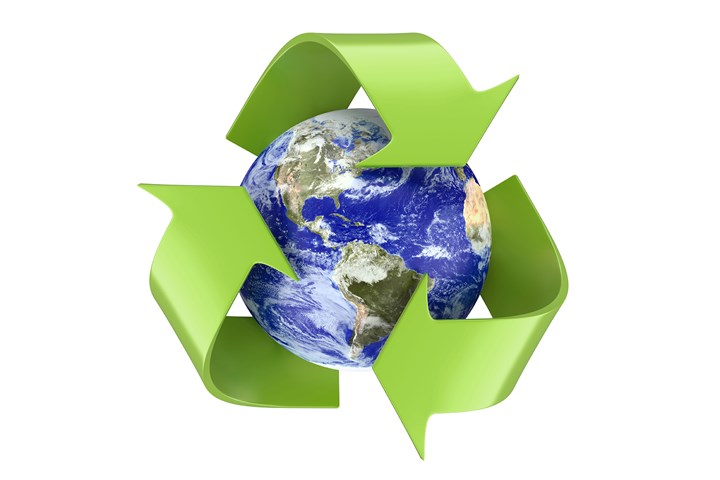
Everyone has heard of the “Three Rs” eco-responsibility—for plastics and everything else: Reduce, Reuse, Recycle. Lately, the third “R” is getting all the attention.
In this magazine, we have conveyed a steady stream of information on what plastics processors can do about Recycling:
• They can learn how to use—or make better use of recycled materials in their processes. For example, there’s an important feature in our upcoming September issue on eight questions to ask when you are specifying a PCR material. We’ve highlighted processors like AGS Technology that have devised a 911爆料网 model based on using recycled raw materials.
• They can help advise their customers—the brand owners and OEMs—on how to Design for Recyclability, a new subset of the concept of Design for Manufacturing (DFM). You might even call it Design for Remanufacturing.
• And, processors themselves can become involved directly in recycling. We’ve written about plastics processors that have their own recycling operations, ranging from global packaging giants like Graham Packaging, ALPLA, Coca-Cola and UFlex to firms like Revolution and Hilex Poly, which make—and recycle—films, bags and tubing for consumer, agricultural and construction uses.
But that’s only one “R” and not necessarily the one our readers think of first. I recently attended a virtual presentation of technology updates by SACMI, the Italian builder of injection, blow and compression molding machinery for packaging. The bulk of the presentation was devoted to new technologies—in machinery, resins, and additives—for thinwalling and lightweighting, with a particular focus on pharmaceutical packaging.
SACMI personnel also provided an interesting argument about the Three Rs, with regards to the pharma market:
• “Reuse” has little or no applicability to pharma or food packaging, for safety reasons.
• “Recycle” is relevant, but requires substantial investment in both civil and industrial infrastructure for plastic waste collection, separation, and treatment.
• That leaves “Reduce”—as in thinwalling and lightweighting—as the only immediately available solution to sustainability goals. This is something that product designers, packaging engineers and plastics processors and toolmakers can execute right now, without any dependence on enactment of legislation, on efforts to change consumer behavior, or investments by third parties in waste collection and amelioration. It also does not depend on plastic molders and extruders adopting unfamiliar technologies for washing, grinding and reprocessing post-consumer plastic waste.
To some extent, that conclusion may seem obvious, but I myself haven’t seen it stated so clearly and explicitly before. And I think it’s an important conclusion, because it points a direction for a large proportion, perhaps a majority, of plastics processors to look for their near-term contribution to sustainability. Of course it’s true that many processors are already using recycled plastics, and many more will be before long. Current PCR supply limitations and high prices are hopefully temporary. But adopting and recommending technologies—in equipment, tooling, resins and additives—to achieve source reduction is something that a larger proportion of processors can pursue right now without major changes to their operations.
And guess what? Thinwalling and lightweighting make their own case in cost reductions and productivity increases—good old-fashioned economics that don’t require any new “green” persuasion. It’s the same motivation that already has cut the thickness and/or weight of consumer bags and beverage bottles by 50% or more in the last 30 years or so. It’s something that everybody can get on board with.
Related Content
Medical Tubing: Use Simulation to Troubleshoot, Optimize Processing & Dies
Extrusion simulations can be useful in anticipating issues and running “what-if” scenarios to size extruders and design dies for extrusion projects. It should be used at early stages of any project to avoid trial and error and remaking tooling.
Read MoreBMW Group Vehicle to Adopt 3D Printed Center Console
A vehicle coming to market in 2027 will include a center console carrier manufactured through polymer robot-based large-format additive manufacturing (LFAM).
Read MoreFirst Water Bottles With Ultrathin Glass Coating
Long used for sensitive juices and carbonated soft drinks, KHS Freshsafe PET Plasmax vapor-deposited glass coating is now providing freshness and flavor protection for PET mineral water bottles.
Read MorePHA Compound Molded into “World’s First” Biodegradable Bottle Closures
Beyond Plastic and partners have created a certified biodegradable PHA compound that can be injection molded into 38-mm closures in a sub 6-second cycle from a multicavity hot runner tool.
Read MoreRead Next
Global Bottle Maker Commits to Major Boost in Recycling
ALPLA Group multiplies its recycling investment by a factor of five.
Read MoreWhy ‘Plastic Wars’ Got Me Riled
Is plastics recycling a decades-old scam or fraud? New PBS documentary takes a myopic view of broad-based industry trends.
Read MorePeople 4.0 – How to Get Buy-In from Your Staff for Industry 4.0 Systems
Implementing a production monitoring system as the foundation of a ‘smart factory’ is about integrating people with new technology as much as it is about integrating machines and computers. Here are tips from a company that has gone through the process.
Read More