Clear, Anti-Fogging PP Lid for Microwaveable Food Packaging
Milliken’s clarifier help food packaging thermoformer convert from OPS to clarified PP.
A clear, anti-fogging PP lid for microwaveable food packaging developed by Taiwan’s South Plastic Industry Co. Ltd. (SPI), a leading Asian manufacturer of thermoformed plastic food packaging, in collaboration with Milliken &Co., has replaced oriented polystyrene (OPS). Many suppliers use OPS for their ready-meal packaging lids, but those can only withstand 185 F/85 C temperatures and are not suitable for microwaveable products.
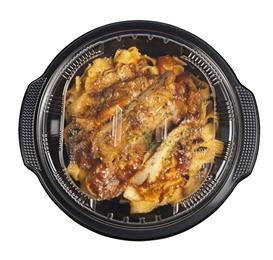
SPI has been striving for years to do this but had not found a way to get PP to meet all performance requirements while also retaining the clarity and non-yellowing aesthetics that are key to consumer appeal. By leveraging on its close, five-year relationship with Milliken, SPI finally achieved its goals. To produce the UltraClear PP resin, the collaborators used Milliken’s Millad NX 8000 clarifier that has been shown to deliver on all the required performance along with processing benefits.
According to SPI president Tosho Wang, by using Milliken’s additives, which also include Hyperform HPN performance nucleating agent in its PP formulations, SPI is now able to thermoform its products at a lower processing temperature, which reduces their energy usage. Moreover, these additives allow SPI to produce a thinner PP lid without affecting rigidity, which in turn helps to reduce plastic usage while increasing output.
SPI, which now uses Milliken clarifiers in all its UltraClear PP packaging products, says it plans to explore using the material to expand the use of PP in more food applications, including some that currently use PET.
Related Content
-
How Compression Ratio Impacts Extruder Performance
Let’s investigate how compression ratio affects performance of an extruder processing LLDPE.
-
Flexible-Film Processor Optimizes All-PE Food Packaging
Tobe Packaging’s breakthrough was to create its Ecolefin PE multilayer film that could be applied with a specialized barrier coating.
-
Polyethylene Fundamentals – Part 4: Failed HDPE Case Study
Injection molders of small fuel tanks learned the hard way that a very small difference in density — 0.6% — could make a large difference in PE stress-crack resistance.