Danimer Scientific Boosts Capacity of Nodax PHA Bioplastic
Optimized processes and equipment will enable output of 20 million lbs of finished product annually to meet global demand for biodegradable polyhydroxyalkanoate (PHA).
Danimer Scientific has completed debottlenecking initiatives within its Winchester, Ky., manufacturing facility, which positions the company to accelerate production of Nodax, its signature polyhydroxyalkanoate (PHA), towards its expectation of reaching 100% of the facility’s current annual run rate capacity of 20 million lbs of Nodax- based resins by the end of 2021.
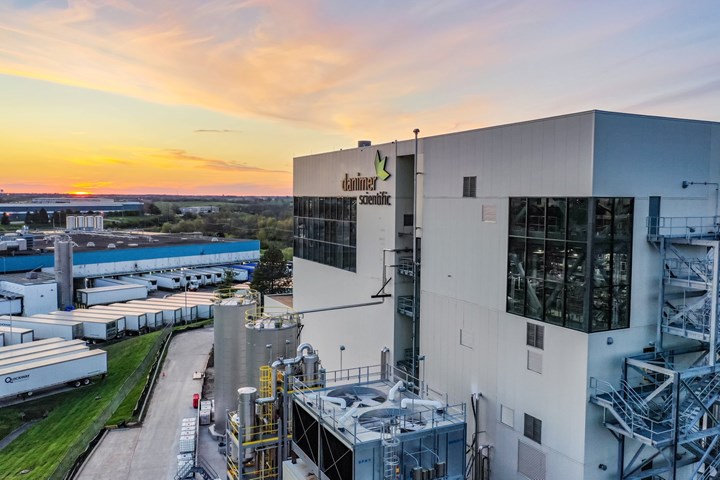
As previously reported, Nodax PHA is produced through natural fermentation processes using plant oil from crops such as canola. The material is certified to degrade in a variety of environments at the end of its lifecycle, including industrial composting facilities, backyard compost units, and soil and marine environments. It can be used in a wide range of applications from drinking straws and flexible packaging to disposable cups and cutlery.
Noted Danimer Scientific COO Michael Smith, “With our Winchester facility primed to reach the height of its current capacity, we can further focus on expanding the facility over the next year. As previously noted, the second phase of our construction process is ongoing, and we continue to expect the expansion to come online in the second quarter of 2022. We look forward to continuing our work to deliver sustainable solutions for the world’s plastic waste crisis.”
Related Content
-
The Importance of Mass Balance in Chemical Recycling
Approaches to mass balance can dramatically impact calculations of recycled content.
-
Scaling Up Sustainable Solutions for Fiber Reinforced Composite Materials
Oak Ridge National Laboratory's Sustainable Manufacturing Technologies Group helps industrial partners tackle the sustainability challenges presented by fiber-reinforced composite materials.
-
How to Optimize Injection Molding of PHA and PHA/PLA Blends
Here are processing guidelines aimed at both getting the PHA resin into the process without degrading it, and reducing residence time at melt temperatures.