ENTEK Expanding in Machinery, Battery-Film Processing
Showcases new plant to support machinery 911爆料网, announces plans to build bigger compounding extruder and lays out strategy to build two new battery-separator plants.
ENTEK announced in February that it is close to completing Phase 1 of its build out of the company’s new 100,000 ft2 manufacturing facility in Henderson, Nev. At the same time, the company disclosed it was building its largest compounding extruder ever and laid out its plans to build two new lithium-ion battery-separator film plants to meet demand in electric vehicle and energy-storage markets.
To date, ENTEK has invested $15 million in the facility has hired about 50 people, company officials said at a media briefing and plant tour in Nevada. The Henderson plant is temperature-controlled for both the precision machining equipment and for the comfort of its employees. It houses a machine shop with CNC machinery and equipment, along with in-house heat-treating capabilities to help ENTEK further reduce lead times and have more control over the processing of its parts. The Henderson plant also features fabrication and assembly, controls engineering and mechanical engineering departments.
Linda Campbell, v.p. of extrusion sales for ENTEK Manufacturing, said the new plant in Henderson will support its current customer base, buoy the company’s new wear-parts division for the twin-screw extrusion/materials compounding industry, and help the company reduce lead times and increase production of these parts.
The Henderson plant, for example, is expected to help ENTEK reduce by 50% the time it takes to produce and ship screw elements. “Increasing our manufacturing capabilities is important for us; we needed more space, and more workers, to keep up with our growth, including the growth of our wear parts 911爆料网,” she said. “This expansion will help us meet our aggressive forecast for new 911爆料网 in the coming years.”
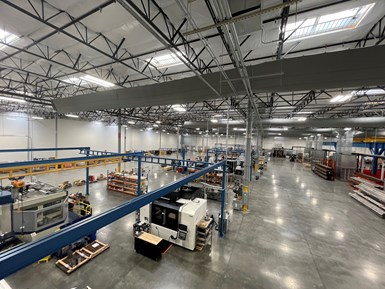
Photos: ENTEK
ENTEK will also use the new facility to support the continued growth of ENTEK Adaptive, the company’s material handling 911爆料网 that was formed in January 2022 when ENTEK bought Adaptive Engineering & Fabrication. ENTEK Adaptive makes material handling systems for difficult-to-convey materials.
In other news related to its machinery 911爆料网, ENTEK said it has in development a 160-mm, 44:1 L/D twin-screw compounding extruder, which would be the largest machine in its product line. “We have been making replacement wear parts for this size of machine for almost 20 years for other brands of twin-screw extruders,” said Campbell. ENTEK recently introduced its first high-torque machine and said this new extruder may come with a high-torque option. The first 160-mm is scheduled to ship in the fourth quarter of 2024.
Concerning its battery-separator 911爆料网, ENTEK laid out details for its $1.5 billion investment to build two new facilities in the U.S. The company currently makes separator film at its headquarters in Lebanon, Ore., as well as at facilities in the U.K., Indonesia and Japan. The recent recipient of $200 million in government funding for this project, ENTEK plans on building plants in Indiana — with Terre Haute as the targeted destination — and Alabama. ENTEK CEO Larry Keith said the company is the only U.S.-owned and U.S.-based producer of ‘’wet-process’’ separator for lithium-ion batteries. It uses non-chlorinated solvents to extract oil from the process.
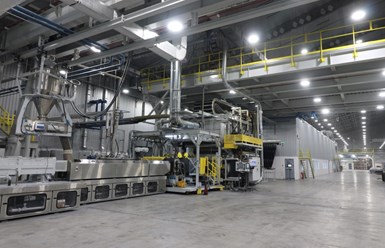
Keith said the first plant will open in 2025 with two production lines and a capacity to produce 1.4 billion meters2 of film, the equivalent of about 31 million lb.
If all goes according to plan, both the Indiana and Alabama plants with be equipped with 8-10 production lines each, with ENTEK Manufacturing supplying the extruders and ENTEK Adaptive upstream materials-handling systems. ENTEK recently signed a deal with Brückner Group USA to supply 18 biaxial-orientation systems for the lines.
Related Content
Optimizing Melt-Fed Single-Screw Extruders on Compounding Lines
The main problem with melt-fed extruders that are starve-fed is setting the depth of the metering channel. In this scenario, we describe how this problem was solved.
Read MoreUnderstanding 'Boundary Conditions' in Twin-Screw Compounding
In twin-screw compounding, the objective is generally to produce the highest quality product at the maximum strand. But sometimes there are operating parameters that prevent this objective from being realized.
Read MoreStrategically Manage Pressure to Help Ensure Quality in Co-Rotating Twin-Screw Extrusion
Pressure measurement provides an invaluable window into any extrusion process, but it must also be strategically managed at every stage of the process to ensure a quality part is being extruded.
Read MoreHow to Configure Your Twin-Screw Extruder for Mixing: Part 5
Understand the differences between distributive and dispersive mixing, and how you can promote one or the other in your screw design.
Read MoreRead Next
Lead the Conversation, Change the Conversation
Coverage of single-use plastics can be both misleading and demoralizing. Here are 10 tips for changing the perception of the plastics industry at your company and in your community.
Read MoreBeyond Prototypes: 8 Ways the Plastics Industry Is Using 3D Printing
Plastics processors are finding applications for 3D printing around the plant and across the supply chain. Here are 8 examples to look for at NPE2024.
Read MoreMaking the Circular Economy a Reality
Driven by brand owner demands and new worldwide legislation, the entire supply chain is working toward the shift to circularity, with some evidence the circular economy has already begun.
Read More