Essentium and Lehvoss Partner to Develop Materials for Additive Manufacturing
Designed specifically for industrial-scale 3D printing.
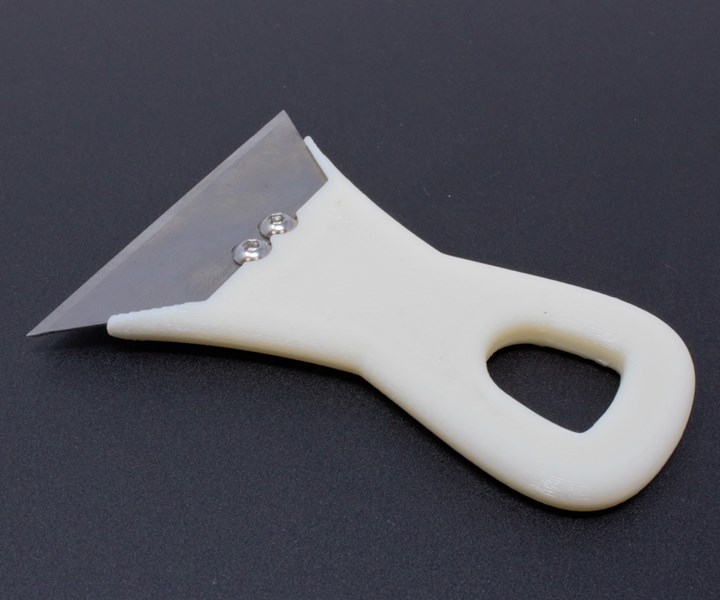
3D-printed scrapper from Essentium.
Essentium Inc. announced it is partnering with Lehvoss Group to develop materials for industrial-scale additive manufacturing. Created specifically for extrusion-based 3D printing processes, the materials meet the standards required for industry applications in aerospace, automotive, oil and gas, biomedical and electronic manufacturing sectors.
The high cost of 3D printing materials has been a significant obstacle hindering additive manufacturing innovation, the company stated. In addition, the low performance of materials optimized but not developed for 3D printing has inhibited additive manufacturing success.
Essentium and ³¢±ð³ó±¹´Ç²õ²õ​â¶Ä‹â¶Ä‹â¶Ä‹â¶Ä‹â¶Ä‹â¶Ä‹ are addressing this challenge by combining ³¢±ð³ó±¹´Ç²õ²õ​â¶Ä‹â¶Ä‹â¶Ä‹â¶Ä‹â¶Ä‹â¶Ä‹’ extensive experience in thermoplastic high-performance compounds with Essentium’s expertise in polymer and composite chemistry to develop engineering-grade materials precisely tuned and certified for a wide range of industry applications.
After two years of collaborative research and development, Essentium has launched a line of PEEK and High-Temperature Nylon (HTN) materials using LUVOCOM 3F compounds. The materials reportedly offer easy printability and non-warping properties, as well as heat and chemical resistance and high mechanical strengths, enabling quality end-parts that can withstand the rigors of the factory floor. Certified on the Essentium High Speed Extrusion (HSE) 3D Printing Platform, the materials are suitable for applications such as mechanical engineering, medical technology and parts subject to high stresses for the engine compartment and drive train in the automotive sector.
Brandon Sweeney, Ph.D., Head of R&D for Materials and Co-founder, Essentium stated: “While there are many compounding companies that optimize materials for 3D printing, few can rival ³¢±ð³ó±¹´Ç²õ²õ​â¶Ä‹â¶Ä‹â¶Ä‹â¶Ä‹â¶Ä‹â¶Ä‹’ manufacturing knowledge and their approach for designing compounds specifically for extrusion-based 3D printing processes. With ³¢±ð³ó±¹´Ç²õ²õ​â¶Ä‹â¶Ä‹â¶Ä‹â¶Ä‹â¶Ä‹â¶Ä‹ we have a true partner who shares our passion in applying material science innovation to accelerate industrial-scale additive manufacturing.
“We have already seen strong demand for our PEEK and HTN materials and look forward to developing new materials that give manufacturers the trust and confidence to shift from prototyping to full-scale production using 3D printing.”
Related Content
-
NPE 2024: Additive Manufacturing Assisting, Advancing Plastics Processing
Exhibitors and presenters at the plastics show emphasized 3D printing as a complement and aid to more traditional production processes.
-
The Connector Conundrum: 3D Printed Mold Tooling’s Role in Innovation
ReelView Fishing faced an electronics obstacle in the development of its new technology for underwater video. Additive manufacturing for moldmaking allowed for the speed necessary to iterate to a solution. How inventors and invention will benefit from new ways of obtaining production-ready tooling.
-
Additive Fusion Technology Optimizes Composite Structures for Demanding Applications
9T Labs continues to enhance the efficiency of its technology, which produces composite parts with intentionally oriented fibers.