Falcon Plastics Expands Tennessee Facility
The South Dakota headquartered custom molder has broken ground on a 20,000-ft2 expansion at its site in Lexington, Tenn., allowing it to add new processing equipment.
Falcon Plastics (Brookings, S.D.) announced that it has begun phase one of a three-phase expansion plan for its Lexington, Tenn. molding facility, breaking ground on a 20,000-ft2 addition that will allow it to install additional equipment. This phase its expected to be completed by the end of summer 2021.
Falcon said the 20,000-ft2 being added in 2021 will be for additional warehousing, allowing two to three injection and blow molding machines to be added. Falcon said its operations team has already begun planning the phase two and three expansions, which will allow more machine additions, eying initiation in 2022.
Founded in 1975, Falcon Plastics is a third-generation family-owned mid- to high-volume custom molder, manufacturing a wide variety of products. The company operates four manufacturing facilities with approximatley 320 employees; more than 120 molding machines; and 300,000-ft2 of space spread over sites in Brookings and Madison, S.D.; Lexington, Tenn.; and Tigard, Ore.; as well as a partnership in a 40,000-ft2 facility in Suzhou, China.
In 2019, Falcon Plastics completed a 27,000-ft2 warehouse expansion, including upgrades and modifications to the manufacturing area of its Madison, S.D. site. In that year, the company also acquired Poly-Cast Inc.—a custom injection molding company outside Portland, in Tigard, Ore. That was the first acquisition in the company’s history.
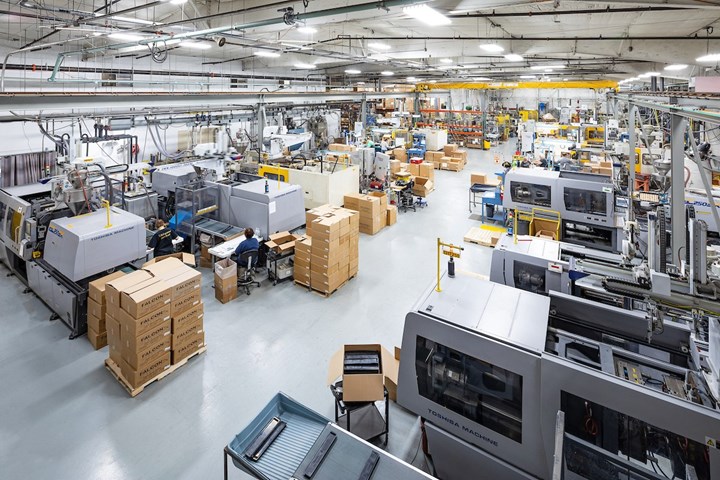
Falcon Plastics has begun an expansion of its facility in Lexington, Tenn.
Photo Credit: Falcon Plastics
Related Content
-
Use These 7 Parameters to Unravel the Melt Temperature Mystery
Despite its integral role in a stable process and consistent parts, true melt temperature in injection molding can be an enigma. Learning more about these seven parameters may help you solve the puzzle.
-
Understanding the Effect of Pressure Losses on Injection Molded Parts
The compressibility of plastics as a class of materials means the pressure punched into the machine control and the pressure the melt experiences at the end of fill within the mold will be very different. What does this difference mean for process consistency and part quality?
-
What to Look for in High-Speed Automation for Pipette Production
Automation is a must-have for molders of pipettes. Make sure your supplier provides assurances of throughput and output, manpower utilization, floor space consumption and payback period.