Schoeneck Containers Is Now Radius Packaging
Name change reflects a broader focus on complete rigid packaging solutions, and keeping customers as the central focus.
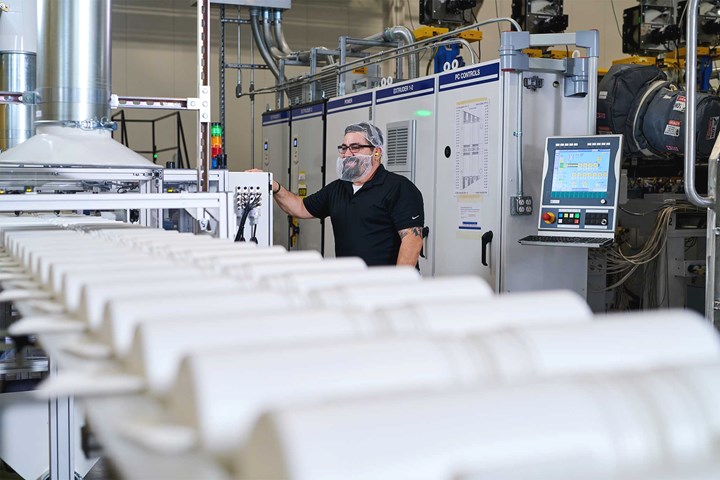
Radius Packaging’s new Delavan, Wis., plant focuses on high-output, highly automated production. (Photo: Radius Packaging)
As it approaches its 50th anniversary this year, Schoeneck Containers, Inc. (SCI) has rebranded itself as Radius Packaging. The custom and stock blow molder of HDPE, PP and PVC containers and injection molder of flip-top caps and tubs has launched a new (radiuspkg.com) to show off its new identity. The company has had its headquarters in New Berlin, Wis., since 1972 and opened a new and larger plant in Delavan, Wis., in 2019. Started by Bob Schoeneck, the formerly family-owned and operated company transitioned to private equity in 2020.
Discussing the new brand, Tom Frank, president and CEO, says, “Over the last 50 years, we continued to evolve our 911爆料网 to meet the needs of our customers; this is what drove our decision to expand beyond blow molded containers with capabilities and services like injection molded closures and labeling that allow us to offer complete rigid plastic packaging solutions.”
Adds Crystal Humphreys, director of marketing, “As we thought about who we are, where we’re headed, and the value we create, we wanted a brand that reflected a promise—to keep our customers at our core, and to the rigid plastic packaging partner that helps our customers connect with theirs, elevate their customers’ experience, and ultimately drive their 911爆料网 forward.”
For full details on Radius Packaging’s current capabilities and its future directions, see the cover story of the upcoming April issue of Plastics Technology magazine.
Related Content
-
First Water Bottles With Ultrathin Glass Coating
Long used for sensitive juices and carbonated soft drinks, KHS Freshsafe PET Plasmax vapor-deposited glass coating is now providing freshness and flavor protection for PET mineral water bottles.
-
Medical Tubing: Use Simulation to Troubleshoot, Optimize Processing & Dies
Extrusion simulations can be useful in anticipating issues and running “what-if” scenarios to size extruders and design dies for extrusion projects. It should be used at early stages of any project to avoid trial and error and remaking tooling.
-
Get Color Changes Right In Extrusion Blow Molding
Follow these best practices to minimize loss of time, material and labor during color changes in molding containers from bottles to jerrycans. The authors explore what this means for each step of the process, from raw-material infeed to handling and reprocessing tails and trim.