All-Electric Shuttle and Stretch-Blow Machines
NPE2024: Meccanoplastica shows off a double-sided shuttle for containers up to 5 L and a reheat stretch-blow molder for up to 2.5 L PET containers with four cavities — both all-electric.
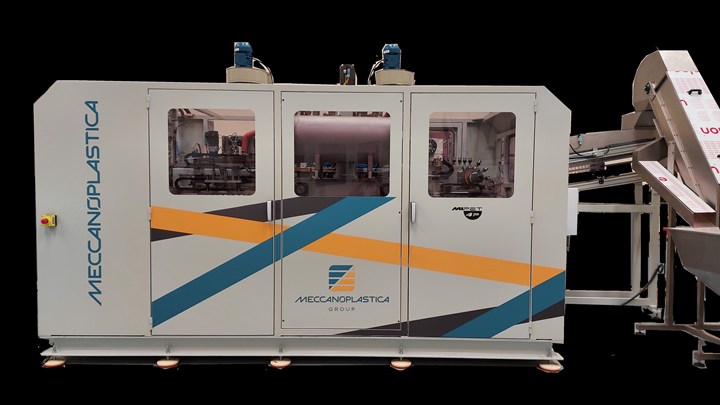
All-electric, four-cavity, linear two-stage stretch-blow MIPET 4P from Meccanoplastica. Source: Meccanoplastica
Meccanoplastica of Italy is highlighting its MIPET 4P all-electric, four-cavity, linear two-stage stretch-blow machine for PET bottles up to 2-2.5 L. One of these units was sold last year to a molder in Florida. Introduced in 2019, it’s designed especially for unconventional bottle shapes; preferential heating is optional. Newer features include a more robust chassis. The machine at the show has a demonstration mold for a 750-ml trigger-spray bottle and can produce up to 1,400 bph per cavity.
Also on display, running only dry cycle, is an all-electric shuttle extrusion blow molder, model HE480D, introduced in 2018. One of the smaller models in the series, it has a 12-metric-ton clamp, 480-mm carriage stroke and 90-mm extruder. This double-station machine can run up to six parisons and mold bottles up to 5 L. The unit on display has a 3+3 parison head with 140-mm center distance.
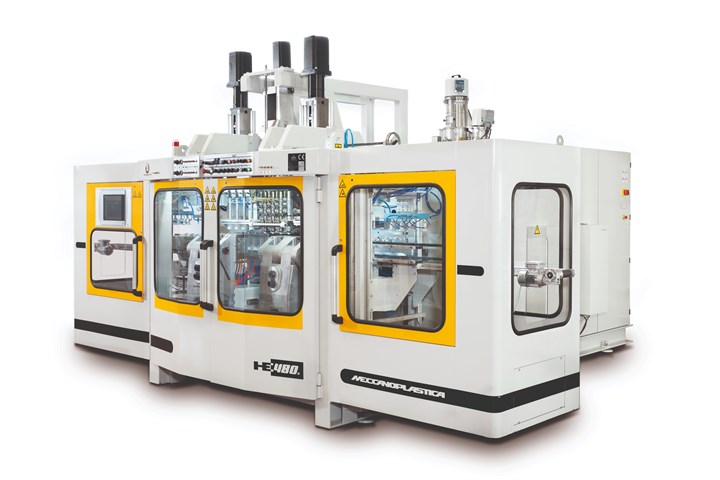
Meccanoplastica’s HE480D all-electric shuttle with 12-ton clamp, 480-mm stroke and 90-mm extruder. Source: Meccanoplastica
Related Content
-
First Water Bottles With Ultrathin Glass Coating
Long used for sensitive juices and carbonated soft drinks, KHS Freshsafe PET Plasmax vapor-deposited glass coating is now providing freshness and flavor protection for PET mineral water bottles.
-
Measuring Multilayer Plastic Containers Made Easier With Today's Ultrasonic Gauges
Ultrasonic gauge technology has evolved to simplify measurement of very thin layers in plastic containers. Today’s gauges with high-frequency capabilities and specialized software can make multilayer container measurement quick and easy for ordinary users.
-
Get Color Changes Right In Extrusion Blow Molding
Follow these best practices to minimize loss of time, material and labor during color changes in molding containers from bottles to jerrycans. The authors explore what this means for each step of the process, from raw-material infeed to handling and reprocessing tails and trim.