Amorphous PEI for Injection-Molded Lenses Used in Co-Packaged Optical Transceivers and Other Optical Connectors
SABIC’s Extem RH1016UCL combines elevated thermal resistance with high strength, broad chemical resistance and more.
An ultra-high-heat, near-infrared (IR)-transparent amorphous PEI grade designed for injection-molded lenses used in co-packaged optical transceivers and other optical connectors has been developed by SABIC. Extem RH1016UCL reportedly is one of the first IR-transparent thermoplastics that can robustly withstand the 500 F/260 C peak temperature of printed circuit board (PCB) reflow soldering while maintaining dimensional stability of the molded part. This capability helps enable optical connectors to be mounted with other components in one step, avoiding the separate assembly and alignment processes that are required for lower-temperature lens materials.
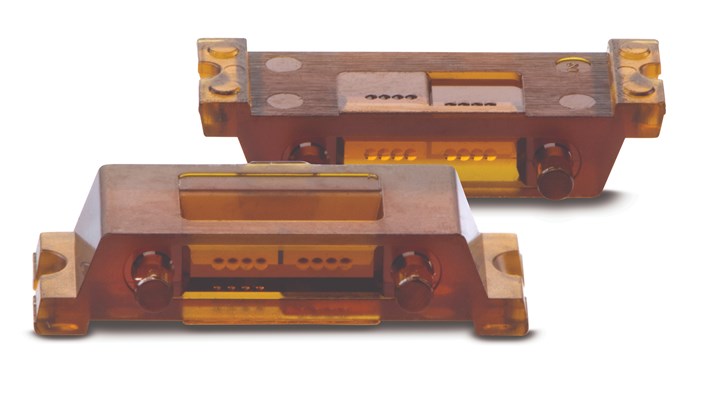
The new Extem resin also boasts high strength, stiffness, and creep performance up to 446 F/236 C, along with broad chemical resistance including chlorinated solvents, and is said to provide high-throughput, precision micro-molding capability for enhanced productivity. Together with optical design freedom and breakthrough high-temperature performance, the resin can help customers transition from pluggable optics to co-packaged optics that support increased data center speed, scale and energy efficiency. Extem RH1016UCL resin has been validated by a major technology U.S. OEM.
According to Florian Jung, global 911爆料网 manager, for Ultem and Extem, co-packaged optics are a next-generation technology that can help increase data center reliability and reduce power usage and costs by bringing the optics much closer to the main switching ASIC (application specific integrated circuit). “Producing complex, miniaturized lenses and arrays for co-packaged optics calls for new materials that can overcome the design, manufacturing scalability and system cost drawbacks of glass. SABIC’s new Extem RH1016UCL resin addresses these needs while helping to advance this emerging technology and opening new opportunities to help improve PCB integration density and energy efficiency,” he said.
Co-packaging reportedly helps make the electronic signal path as short and seamless as possible to facilitate very high data transmission rates. SABIC’s global technology centers provide micro-molding capabilities, including state-of-the-art equipment to test the material’s optical properties and constants, metrology, reflow soldering stability and application (hydro)aging.
Related Content
-
The Fantasy and Reality of Raw Material Shelf Life: Part 2
For the vast majority of thermoplastics, the stability of the materials can be stated in years, not months. But there are exceptions where shelf life can be a serious issue.
-
Polymer Showdown — PC/ABS vs. PC/PBT — May the Best Material Win
First in a series, experts from plastics engineering consultancy The Madison Group will pit leading thermoplastics against each other to see how they differ in processing characteristics, chemical resistance, thermal and mechanical performance, and more.
-
Polymer Science for Those Who Work With Plastics: Why Entanglements — Not Just Molecular Weight — Drive Plastic Performance
Ever try running your fingers through tangled hair? Yeah … that’s not fun, but that’s what happens at the molecular level when polymer chains reach the right length. They wrap around each other, intertwine and … get stuck — and those tangles are the real reason plastics perform the way they do.