Extrusion: Enhanced Continuous Belt Screen Changer
Parkinson Technologies has upgraded its Key Filters brand of KCH continuous belt screen changer to make them more robuts, faster, more reliable and easier to maintain.
Parkinson Technologies has upgraded its Key Filters brand of KCH continuous belt screen changer to make them more robuts, faster, more reliable and easier to maintain.
To increase overall robustness, vital machine sensors are now guarded, moved further away from high-heat locations and upgraded to meet extreme production environments. The puller sensor, for example, was upgraded from a string potentiometer to an extreme-duty, non-contact inductive sensor.
Additional advancements include increased cooling through the inlets and outlets, resulting in three times the flow rate compared to the previous version. This cooling enhancement accelerates the formation of the sealing plug, which allows the KCH to advance the screen at an even quicker rate, thus filtering out higher volumes of contaminants and reducing the risk of downtime due to seal failure.
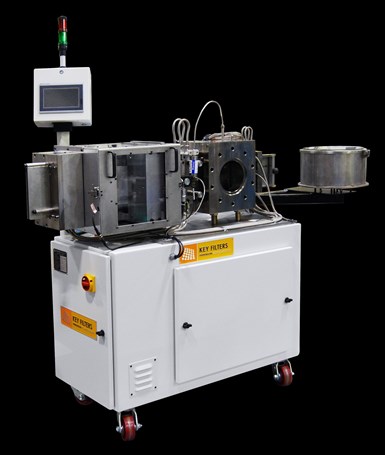
When working with heated polymer in a real-world scenario, situations arise in an extrusion facility outside of the screen changer’s control that may cause significant down-time and damage to the machine. This is often due to accidentally increasing the screw speed on the extruder too quickly at start-up or interruption in the cooling water to the screen changer which results in a loss of the sealing plug in the screen outlet. The Key Filters team looked at ways to reduce potential down-time to these unfortunate situations by separating the puller and outlet assemblies. The heated polymer will bypass the puller assembly, eliminating component damage and providing an easier clean-up if plug loss occurs. An extrusion line can be fully operational in just a fraction of the time.
Related Content
-
The Importance of Barrel Heat and Melt Temperature
Barrel temperature may impact melting in the case of very small extruders running very slowly. Otherwise, melting is mainly the result of shear heating of the polymer.
-
What to Know About Your Materials When Choosing a Feeder
Feeder performance is crucial to operating extrusion and compounding lines. And consistent, reliable feeding depends in large part on selecting a feeder compatible with the materials and additives you intend to process. Follow these tips to analyze your feeder requirements.
-
How to Select the Right Cooling Stack for Sheet
First, remember there is no universal cooling-roll stack. And be sure to take into account the specific heat of the polymer you are processing.