Extrusion: Enhanced Deckle Boosts Coating Productivity
Simplified mechanisms for Nordson EPC die streamline the adjustment of coating width while reducing the size of edge bead.
Nordson has streamlined the design of the EPC deckle system for EDI extrusion coating and laminating dies to make it easier to control edge bead and reducing downtime for width changes and cleaning.
The widely used EPC die includes an internal deckle system that reduces resin cost and trim waste by controlling edge bead formation, plus an external deckle for convenient width adjustment. The new enhanced design provides these improvements:
● Easier control of edge bead: For independent adjustment of the internal deckle components, Nordson has replaced a rack-and-pinion gear with a threaded stud that makes it easier to fine-tune the edge bead, reducing the amount of trim required and increasing material savings.
● Easier manual adjustment of deckle width: Nordson has replaced a gear box used for adjusting overall deckle width with a nut on the adjustment rod, reducing the width and weight of the deckle system and increasing access for operators.
● More robust and user-friendly construction: A durable new deckle rod support guide makes deckle adjustment easier.
● Easier access for cleaning and maintenance: A low-profile external deckle can be removed as a single unit, or it can slide out for installation of a lip scraper without removal of the entire deckle assembly. Similarly, internal deckle components can be taken out by removing six bolts from the end of the deckle system without disengaging the entire unit.
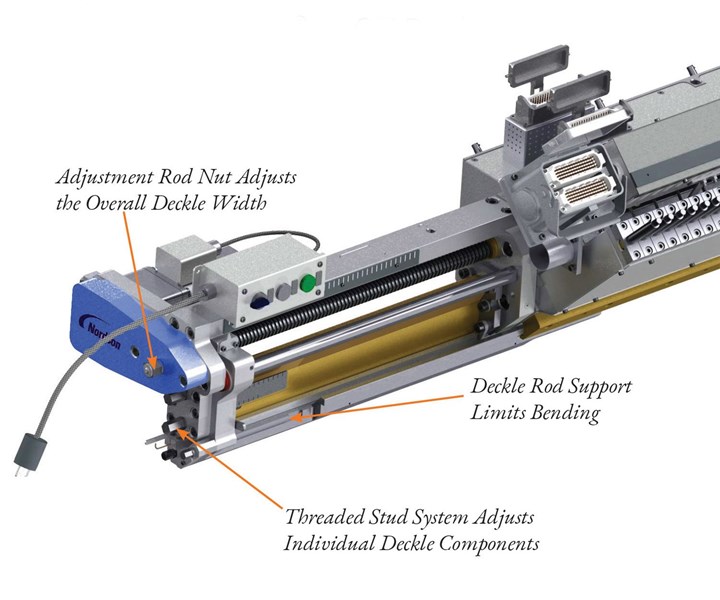
The internal deckle system in an EPC die provides fine-tuning of the edge profile of a coating. The molten polymer in a die without an EPC deckle system will exhibit transverse flow, producing an enlarged edge bead from the resulting necking at the die exit. In the EPC system, the internal deckle components for adjusting the edge bead profile are located downstream of the primary manifold—one in the preland section, the second in the secondary manifold. By adjusting the positions of these components relative to one another, it is possible to reduce the flow of polymer at the extreme edges of the coating, thereby minimizing edge bead.
Related Content
-
Medical Tubing: Use Simulation to Troubleshoot, Optimize Processing & Dies
Extrusion simulations can be useful in anticipating issues and running “what-if” scenarios to size extruders and design dies for extrusion projects. It should be used at early stages of any project to avoid trial and error and remaking tooling.
-
Shredding Thin Film: How to Do It Right
While many processors recoil at this task, a little know-how in shredding equipment, processing, and maintenance should add the necessary confidence.
-
How To Identify Resin Degradation in Single-Screw Extruders
Degradation can occur in many single-screw extrusion operations, and typically occurs due to minor design flaws in the screw. Here is how to track it down.