Fakuma: Molding Machine and Simulation Software Interface Expanded
Engel’s sim link data interface for two-way exchange of simulation and process data between Engel machines and simulation programs has been extended to include Simcon’s CADMOULD program.
Injection molding machine and automation supplier Engel has expanded its sim link interface, which allows Engel presses to interchange with molding simulation software, to include Simcon’s CADMOULD software. When the capability was introduced at K 2019, Engel said sim link was compatible with Autodesk’s Moldflow program. At the Fakuma 2021 show, Engel said it is expanding the range of applications that sim link can support in response to positive customer feedback and growing demand. Simcon, based in Wuerselen, Germany, is focused on molders outside the U.S. and Canada, with resellers and regional partners throughout Europe and the Middle East, in addition to Mexico and Brazil.
In a release, Simcon noted that injection molding simulations can capture process parameters in a different format then they would be entered into the press, forcing process technicians to translate the information into a format the machine can utilize. Further, if the real-world process is tweaked from what the simulation called for, those changes often never get back to the engineers that ran the simulation, limiting their ability to learn what needed to be adjusted. sim link not only translates the simulation software into parameters the machine can understand, but it records and saves any changes to the process compared to what the simulation called for so the engineers can see how what CADMOULD called for differs from the real-world molding of the part.
The companies said CADMOULD support is currently being beta tested at customers sites with a general commercial release scheduled for early 2022.
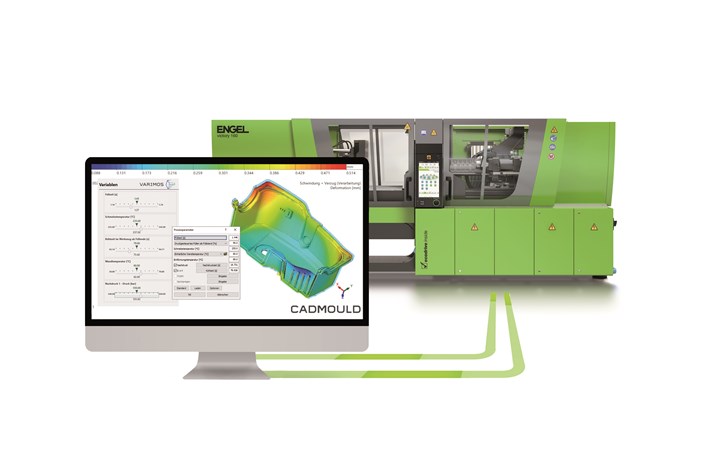
Engel’s sim link platform now supports Simcon’s CADMOLD injection molding simulation software.
Photo Credit: Engel
Related Content
-
Use These 7 Parameters to Unravel the Melt Temperature Mystery
Despite its integral role in a stable process and consistent parts, true melt temperature in injection molding can be an enigma. Learning more about these seven parameters may help you solve the puzzle.
-
Using Data to Pinpoint Cosmetic Defect Causes in Injection Molded Parts
Taking a step back and identifying the root cause of a cosmetic flaw can help molders focus on what corrective actions need to be taken.
-
Process Monitoring or Production Monitoring — Why Not Both?
Molders looking to both monitor an injection molding process effectively and manage production can definitely do both with tools available today, but the question is how best to tackle these twin challenges.