Fakuma: Temperature Controller Targets Large, Heavy Molds
Wittmann says its Tempro Basic Large 120 temperature controller pairs high heating capcity and flow rates for optimized heating and cooling of bigger tools.
Wittmann Battenfeld is introducing the Tempro basic Large 120 temperature controller at Fakuma (Oct. 12-16; Friedrichshafen, Germany; Hall B1, Booth No. 1204) with a maximum heating capacity of 36 kW. Wittmannn says that capacity can ensure an optimal heating time, especially in instances where very fast heating is necessary—like after a mold change.
To further support homogenous heat transfer, the Tempro basic Large 120 can be optionally equipped with a new frequency-controlled pump. This pump model, known as the SpeedDrive, comes with an output of 4 kW and can handle a maximum flow rate of 300 l/min (79 gpm), generating a maximum pressure of 5 bar (72.5 psi). With the SpeedDrive pump, users can establish parameters for further process regulation, including motor speed, flow rate, pump pressure and differential temperature. This includes automatic adjustment of the parameter settings within a preestablished tolerance margin.
Wittmann says the Tempro basic Large 120 was developed in response to a growing demand in the market for fast heating of large molds, while still meeting high cooling performance standards. As an example of the unit’s cooling performance, Wittmann notes it has achieved a differential temperature of 60C (140F) between mold water and cooling water from a high cooling performance of 175 kW. As an additional option, a stainless steel vortex flow measurement device is available for the temperature controller, with a measurement range from 20 to 400 l/min (5 to 106 gpm).
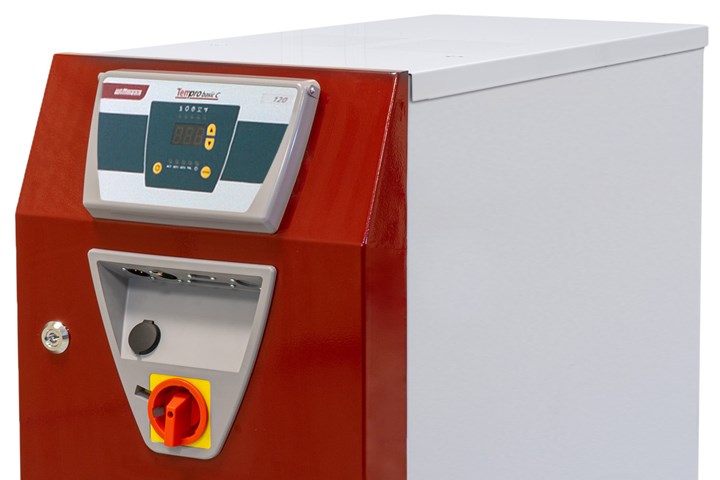
Wittmann Battenfeld’s new Tempro basic large 120 temperature controller is targeting rapid heating and cooling of large molds.
Related Content
-
North American Distribution for System to Track Cooling-Circuit Temperatures, Flow Rates
Globeius is now a North American supplier of Mouldpro’s Flosense 1.0 Flexible Flow Monitoring system for tracking manifold pressures and mold temperatures.
-
Captive Molder Beefs Up Auxiliaries to Boost Quality, Consistency
SeeScan adds conveying, drying, feeding and chilling technologies to improve quality — and enhance employee safety — in production of its underground/underwater inspection systems.
-
Water Temperature Control Upgraded and Integrated into Machine Control
Engel’s new eco-flomo temperature control system continuously monitors injection mold cooling and temperature control circuits, displaying pressure, temperature and flow rate values.