Material Handling: Dense-Phase Pneumatic Conveying Offers Gentler Material Movement
Gericke USA says proprietary design of the Pulse-Flow pneumatic conveying system utilizes regular pulses to form the dry material into separate, pulsed slugs.
Gericke USA says its new Pulse-Flow PTA dense-phase pneumatic conveying system is ideal for moving fragile, free-flowing and cohesive powders, granulates, and coarse-grained products, including plastics. The Pulse-Flow PTA directs the air or nitrogen into the pressure vessel and pipeline in timed pulses, creating a gentle conveying action at high pressures with low gas velocities to safely convey sensitive products in mass flow up to 500 feet.
Gericke told Plastics Technology that pressure in the system varies depending on the conveying distance and number of bends in the line. As an example, Gericke says if you assume a total line length of 50 m with 5 bends, then the expected conveying pressure will be around 1 to 1.5 bar. In terms of how the Pulse-Flow PTA dense-phase differentiates itself from similar technologies, Gericke says the product plug is initiated at the starting point and no further external air injectors along the pipeline are required. Gericke also uses a
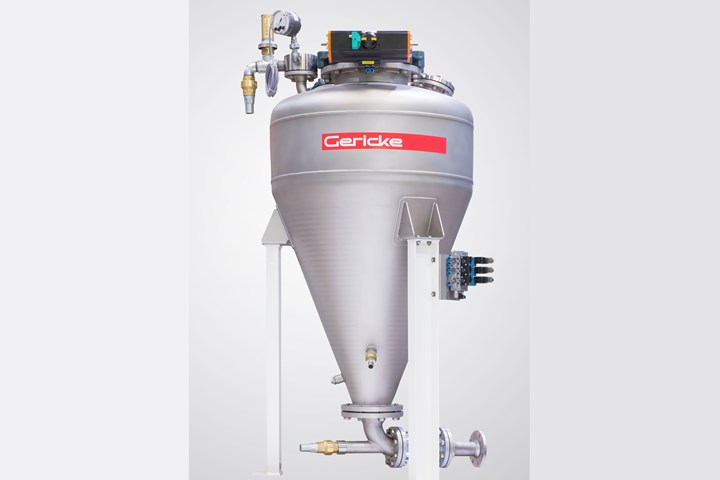
Gericke USA says its new Pulse-Flow PTA dense-phase pneumatic conveying system can safely move sensitive products in mass flow up to 500 feet.
controlled air flow system to maintain the correct conveying speed. The system’s capacity or throughput depends on several factors, including conveying distance, conveying velocity and pipe diameter. Achievable instantaneous conveying capacities are between 20 to 40 tons/hr.
Gericke says the system can be custom engineered for each application, matching the product design to the desired throughput rates, conveying distances, and other requirements in either batch or continuous operation.
Related Content
-
Deflection Elbows Eliminate Streamers for Large Film Processor
New elbows eliminate troublesome streamers to increase productivity at leading blown film processor.
-
Cut Loading Time Through Direct Charge Blending
Direct charge blender loading, a vacuum-powered automation process, can dramatically improve loading time and reduce material costs. In this article, we address ten common questions to help you determine if the systems are right for your facility.
-
Safety, Recycling, and Compounding Trends Bring New Opportunity to 70-Year-Old Company
NPE2024: Vac-U-Max presents pneumatic conveying solutions for powdered materials.