Medical-Tubing Extruders Redesigned
Sleeker models simplify cleaning, maintenance, and operator accessibility.
Davis-Standard has upgraded its MEDD line of medical-tubing extruders to simplify cleaning, maintenance, and operator accessibility.
The MEDD is Davis-Standard’s signature extruder for tight-tolerance medical tubing applications, including microbore, multi-lumen and catheter tubing. Operational advantages include a compact footprint, interchangeable barrel assembly, linear machine movement, a replaceable feed-section liner, Windows PLC control system, and the capacity to process a broad range of thermoplastic materials and high-temperature resins.
“The new MEDD design is essentially a more sophisticated version of our first model,” notes Kevin Dipollino, sr. product manager for Davis-Standard’s Pipe, Profile and Tubing 911爆料网. “The electrical enclosure/machine base and cigar hood are now stainless steel to provide smoother surfaces for easier cleaning. In addition, we improved cable management throughout with specified cable lengths, cable storage, defined cable routing and an improved configuration. We also added access flip-down doors for easy access to simplify material draining and accessibility when changing the barrel.”
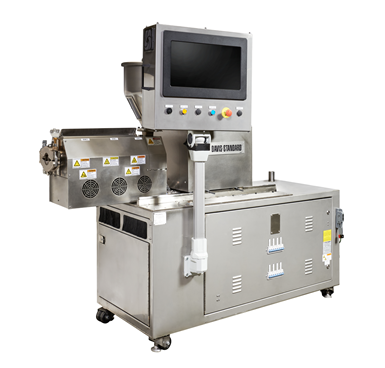
The ability to quickly change barrels for faster material change over or different diameter barrels is a significant benefit of the MEDD. This extruder design has a horizontal slide to easily move the motor and barrel section to mate to the customer downstream and a cantilevered feature at the front of the extruder for loading and unloading the barrel onto a cart during changeovers. Additionally, the new model also has a bidirectional hood vent to improve air circulation.
The MEDD is available in three product ranges: ¾ –1 in., 1–1.25 in., and 1.25–1.5 in. In addition, Davis-Standard’s state of the art Technical Center in Connecticut, which is equipped with MEDD extruders, is also available for R&D.
Related Content
-
How Polymer Melts in Single-Screw Extruders
Understanding how polymer melts in a single-screw extruder could help you optimize your screw design to eliminate defect-causing solid polymer fragments.
-
Roll Cooling: Understand the Three Heat-Transfer Processes
Designing cooling rolls is complex, tedious and requires a lot of inputs. Getting it wrong may have a dramatic impact on productivity.
-
How to Select the Right Tooling for Pipe Extrusion
In pipe extrusion, selecting or building a complementary set of tooling often poses challenges due to a range of qualitative factors. Here’s some guidance to help you out.