Movable Tempering Stamp Can Eliminate Surface Defects
NPE2024: Incoe says Heat-Inject Technology introduces localized heat to remove weld or knit lines, or help melt flow into hinges, thin walls, delicate geometries or microstructures.
Incoe says Heat-Inject Technology enables a part’s surface quality and cavity filling to be optimized via localized mold temperature control with targeted heat pulses. In addition to reducing knit lines that form around holes and openings on a part, Incoe says Heat-Inject can also improve melt flow through cold runner fan gates or thin-wall sections of the cavity. An add-on module for Incoe’s unitized manifold systems, Heat-Inject features simple design and implementation, eliminating larger mold modifications and the higher costs associated with alternative solutions to such surface defects. It also features low power consumption — only 220V AC/30-amp power input is required.
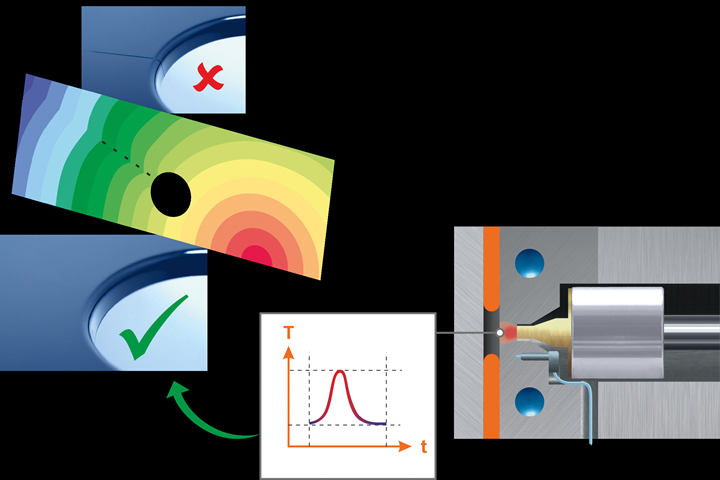
Incoe’s Heat-Inject introduces heat to the cavity wall in areas where it can assist with surface defects, like knit lines. Source: Incoe
Based on the patent-pending Z-system from Incoe partner Hotset, Heat-Inject is not an additional heater, but a movable tempering stamp, with a heated tip that introduces a heat pulse by briefly pressing against the rear wall of the cavity. With this technology, weld lines and flow lines are technically still there, but they’re no longer visible on the surface.
At the show, Incoe is featuring a hot runner and mold equipped with Heat-Inject, as well as the company’s Flight Attendant technology, running on an all-electric LS Mtron LSG-240 E injection molding machine with a Sepro robot. Three through-holes in transparent components will demonstrate Heat-Inject’s elimination of knit lines. The company is also showcasing its ZTT valve-gate hot runner and the I-Series Pro and GSC2 Mini controller technologies.
Related Content
-
Breaking News From NPE2024
Here is a firsthand report of news in injection molding, extrusion, blow molding and recycling not previously covered.
-
Real-Time Production Monitoring as Automation
As an injection molder, Windmill Plastics sought an economical production monitoring system that could help it keep tabs on its shop floor. It’s now selling the “very focused” digital supervisor it created, automating many formerly manual tasks.
-
Thin, High-Performance Nylon/PE Barrier Film for Thermoformed Packaging
Südpack’s Multifol Extreme film is well suited for greasy, protein-rich and frozen foods