Software Reduces Print Iterations and Optimizes Part Designs in Additive Manufacturing
Startup company Araqev’s software applies machine learning to nominal design files and scanned point cloud data from printed products to simulate deviations and modify designs.
Araqev (West Lafayette, Ind.) says its software can help users print products in only a few design iterations, reducing scrap material and machining time while improving satisfaction with the final printed products. Founded by Arman Sabbaghi, associate professor in Purdue University’s Department of Statistics in the College of Science, Araqev starts by having users upload their nominal design files and scanned point cloud data from their printed products.
The software then uses these inputs to fit machine learning models that can simulate shape deviations for future printed products and calculate modifications to the nominal designs so that when the revised designs are printed, they reportedly exhibit fewer shape deviations compared to the original.
Araqev says its algorithms also transfer knowledge over time via machine learning models across different materials, printers and shapes. The company says it verified the software’s performance in two validation experiments using a Markforged Metal X 3D printer running 17-4 PH stainless steel. Araqev reported that its algorithms reduced shape inaccuracies in those instances by 30-60%. On the company’s website, it says it has consistently achieved high quality prints in one or two design iterations over more than a dozen case studies using four different printers.
Araqev is establishing direct partnerships with 3D printing manufacturers and companies, seeking to sell licensing contracts for its program.
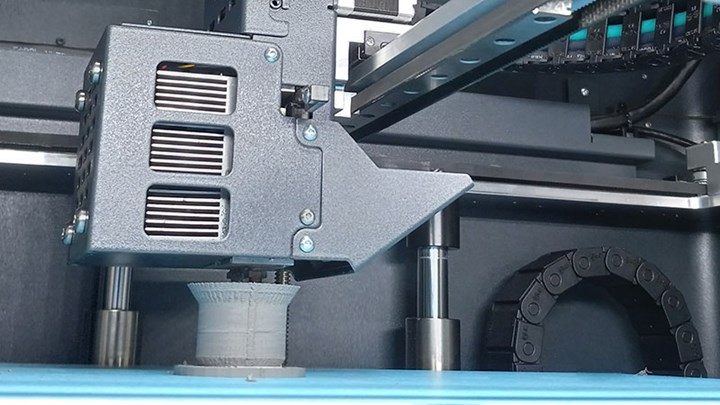
A Markforged Metal X 3D printer creates a stainless-steel tool in Purdue University’s Herbert C. Brown Laboratory of Chemistry after utilizing Araqev to optimize the design.
Photo Credit: Araqev
Related Content
-
5 Trends in 3D Printed Injection Mold Tooling
3D printing has moved beyond conformal cooling, and is now being applied to injection molds more broadly. Observations on additively manufactured mold tooling from the Plastics Technology Expo — PTXPO 2025.
-
Smooth Operators: Vibration Compensation Improves Robot Performance
Ulendo is working to apply its vibration compensation algorithm to robots. This application is more complex than its initial market of fused filament fabrication 3D printers, but could result in faster, cheaper robots.
-
Additive Fusion Technology Optimizes Composite Structures for Demanding Applications
9T Labs continues to enhance the efficiency of its technology, which produces composite parts with intentionally oriented fibers.