System Takes Aim at Food-Packaging Applications
Gneuss will present new recycling system at the K Show this October.
Gneuss will show a new complete recycling system, the Omni series, at K Show 2022 in Dusseldorf. Targeting PET thermforms, the Omni has a capacity of 450 lb/hr and consists of the following components:
- A 3C feeder with rotating knives inside cut, compact, and precondition the material, beginning the heating and degassing process upstream of the extruder. Low density materials can be fed without the need for external processing steps.
- An extruder, called the MRS Jump, is based on Gneuss’s multiple rotating screw technology. It features a longer multiple rotation section that promises longer residence time and more surface area exchange under vacuum. This will reportedly enable enhanced devolatilization of PET to meet the stringent requirements of food contact standards. The powerful vacuum system manages the viscosity despite variation in properties, eliminating the need for liquid state polycondensation and making it especially valuable for reclaimed materials.
- The RSF Genius, which is a rotating filter with automatic backflushing for self-cleaning. Screens can be re-used up to 400 times and mesh can be above 1200. Quality assurance is provided by an online viscometer, VIS.
The Omni series can be customized for specific materials. Samples will be on display of food grade PP tubs and PS sheet, both made from 30% PCR.
At Gneuss’ headquarters in Bad Oeynhausen, Germany, the company will be demonstrating two other Omni lines. An Omni Max machine set up to run sheet extrusion will be running at the technical center, which will be open to visitors. In addition, an Omni Boost machine with Jump polyreactor will be running. The Jump polyreactor is an LSP system that can raise intrinsic viscosity of PET melt.
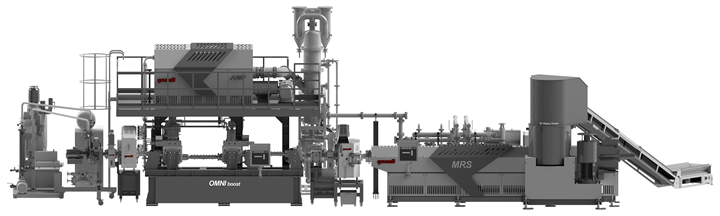
The Omni Boost system with (left to right) 3c feeder, MRS extruder, and Jump polyreactor. This system will be running at Gneuss Headquarters during K Show 2022. Photo Credit: Gneuss
Related Content
-
The Importance of Barrel Heat and Melt Temperature
Barrel temperature may impact melting in the case of very small extruders running very slowly. Otherwise, melting is mainly the result of shear heating of the polymer.
-
Part 2 Medical Tubing: Use Simulation to Troubleshoot, Optimize Processing & Dies
Simulation can determine whether a die has regions of low shear rate and shear stress on the metal surface where the polymer would ultimately degrade, and can help processors design dies better suited for their projects.
-
Understanding Melting in Single-Screw Extruders
You can better visualize the melting process by “flipping” the observation point so the barrel appears to be turning clockwise around a stationary screw.