Tunnel Gate Inserts Gain U.S. Distributor
Distributed by PCS Company, i-mold’s tunnel gate inserts allow automatic degating of parts from the runner system during ejection and can hide gate marks on a part’s underside.
PCS Company is now distributing tunnel gate inserts in the U.S. from Erbach, Germany-based i-mold Molding Innovations. Founded in 2004, i-mold’s focus is on tunnel gate technology and demolding. Developed and produced in-house at i-mold, PCS says the tunnel gate inserts can provide high savings potential for moldmakers and injection molders by eliminating secondary operations or other means of degating.
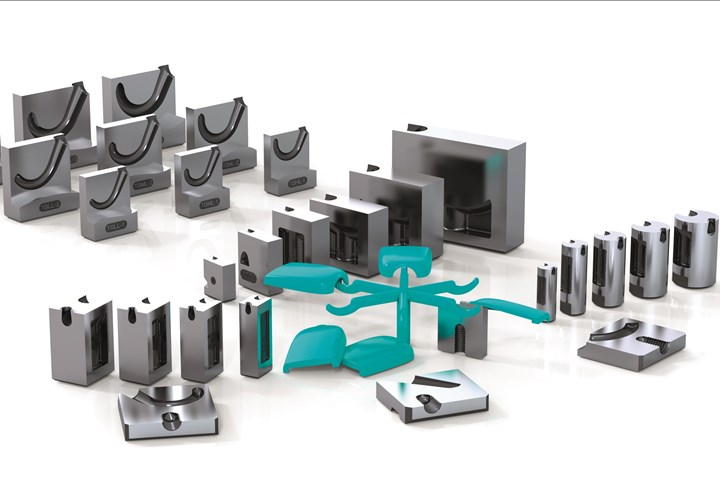
Made via metal injection molding, i-mold says the dimensions of its tunnel gate inserts remain consistent from component to component.
Photo Credit: PCS Company
Also known as ‘cashew’ or ‘banana’ gate inserts, the tunnel gate inserts allow automatic degating of parts from the runner during ejection, and they can also can be used to hide gate marks on the underside of the molded part.
Made of M2 tool steel using metal injection molding (MIM), PCS says the i-mold inserts feature smooth feed channels and precise gate sizes that are repeatable from insert to insert. PCS adds that the inserts are suitable for all plastics thanks to their optimized feed channel geometry, including the ability to work with up to 60% filled materials.
Related Content
-
Got Streaks or Black Specs? Here’s How to Find and Fix Them
Determining the source of streaking or contamination in your molded parts is a critical step in perfecting your purging procedures ultimately saving you time and money.
-
Injection Molding: Focus on these Seven Areas to Set a Preventive Maintenance Schedule
Performing fundamental maintenance inspections frequently assures press longevity and process stability. Here’s a checklist to help you stay on top of seven key systems.
-
Understanding the Effect of Pressure Losses on Injection Molded Parts
The compressibility of plastics as a class of materials means the pressure punched into the machine control and the pressure the melt experiences at the end of fill within the mold will be very different. What does this difference mean for process consistency and part quality?