Wittmann Finds Battery Partner for Direct Current (DC) Molding Machine Concept
Displaying the solar-powered press at Fakuma 2023 following its K 2022 debut, Wittmann announced a development partnership with Innovenergy for DC infrastructure.
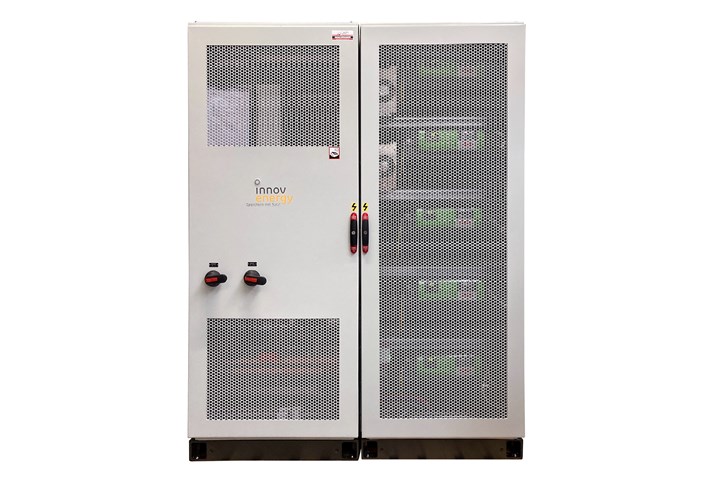
Solar power storage system consisting of salt-battery technology from innovenergy. Photo Credit: Wittmann Battenfeld
After debuting the concept of an injection molding machine running off renewably sourced direct current (DC) at K 2022, Wittmann Battenfeld once again promoted the technology and a battery collaboration partner at Fakuma 2023. At the show, an EcoPower B8X series, powered via a solar power storage battery, molded a polypropylene drainage body from a single-cavity tool supplied by Kunststofftechnik Grabher GmbH. The part was removed by a modified Wittmann WX142 robot also equipped to utilize DC energy.
At the live Fakuma presentation, the machine was disconnected from the exhibition hall’s grid, but was instead powered independently via Innovenergy’s solar power storage salt battery. To balance the brief load peaks of the injection molding machine, additional electrochemical capacitors, known as super-caps, were used to complement the sodium-nickel storage batteries. The battery has a total capacity of more than 45 kWh, which was more than sufficient for continuous machine operation throughout the 8-hour trade fair day.
Wittmann said that since it first presented the technology, it has taken further developmental steps, including finding a partner specializing in DC infrastructure: Swiss firm Innovenergy. That company has been developing and operating energy storage systems with salt batteries for almost 10 years, originally creating sodium-nickel technology for e-mobility, but more recently entering the stationary storage battery sector. The Innovenergy batteries range in storage capacity from 9 to 999 kWh, with inverter capacities from 3 to 300 kVA. Focused on the industrial sector, the company has installed roughly 1,000 salt-battery storage systems to date. Innovenergy says key factors in the industrial space include energy efficiency, connected load limitations of AC infrastructures, independence and the potential for failure safety in cases of power interruption.
To address these, Innovenergy markets its DConnect system featuring renewable energy generators, powered by photovoltaics or wind, and energy storage batteries that are linked with each other in a separate DC network. The company says this enables direct use of the generated energy with greatly reduced conversion loss, and only surplus electricity returns to the power network. Overall, Innovenergy says DC/AC/DC conversion losses between the solar power station and the machine can be lowered by up to 15%.
In addition to lowering energy costs and helping preserve the environment, Wittmann notes that using a machine that applies energy generated by an in-house solar power station enables molders to store direct current in batteries, avoiding expensive current peaks and improving power supply reliability.
The company says its all-electric EcoPower, equipped with highly dynamic servo motors, is well suited for use in a DC power network. The machine comes with the patented KERS — kinetic energy recovery system — as standard, enabling it to convert kinetic energy from machine movement into electric energy during deceleration processes and further reducing energy consumption.
Wittmann says that also applies to a DC-compatible robot powered directly via the DC voltage interim circuit of the EcoPower. The robot returns any surplus energy to the interim circuit whenever its axes are decelerated. If the machine operates in a DC network, the deceleration energy can also be fed back into the network, enabling other connected machines to be powered by this energy or to store it in batteries.
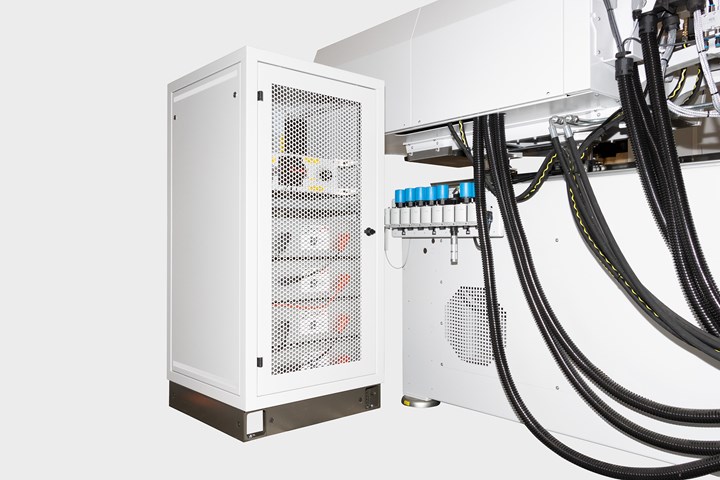
This “super caps” system was used to cover brief load peaks. Photo Credit: Wittmann Battenfeld
Related Content
Process Monitoring or Production Monitoring — Why Not Both?
Molders looking to both monitor an injection molding process effectively and manage production can definitely do both with tools available today, but the question is how best to tackle these twin challenges.
Read MoreHow to Design Three-Plate Molds, Part 1
There are many things to consider, and paying attention to the details can help avoid machine downtime and higher maintenance costs, and keep the customer happy.
Read MoreUsing Data to Pinpoint Cosmetic Defect Causes in Injection Molded Parts
Taking a step back and identifying the root cause of a cosmetic flaw can help molders focus on what corrective actions need to be taken.
Read MoreThree Key Decisions for an Optimal Ejection System
When determining the best ejection option for a tool, molders must consider the ejector’s surface area, location and style.
Read MoreRead Next
Fakuma 2023: Wittmann Battenfeld Expands All-Electric Line, Direct-Current Capabilities
Wittmann Battenfeld will introduce the new EcoPower B8X injection molding machine line and show direct current as an energy source for a concept machine that will power its own robot.
Read MoreOn Site: 140 Years…And Growing Stronger
Now in its fifth generation of family ownership, this sheet extruder isn’t all about output. Its focus is on creating solutions in highly customized markets that aren’t immediately associated with sheet.
Read More