‘Contactless’ Accumulator Is Gentle to Superthin PET Bottles
Sidel’s Gebo AQFlex protects ultralight PET water bottles from dents at Suntory Japan.
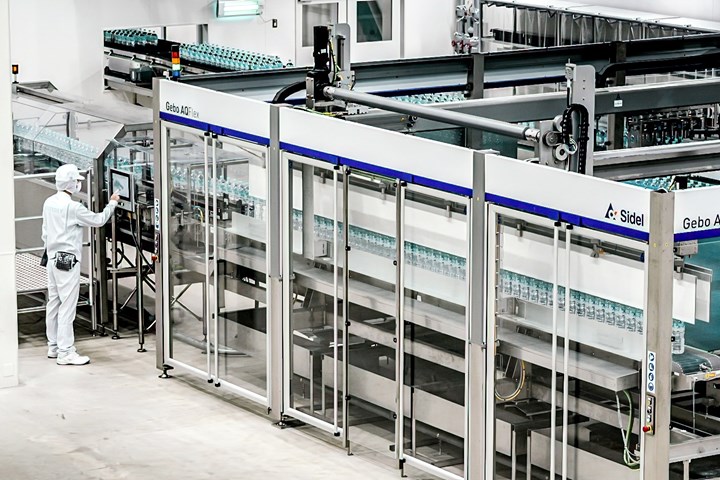
Suntory Japan’s newest plant bottles mineral water using Sidel’s Gebo AQFlex compact, all-in-one conveying/accumulating system. (Photo Credits: Sidel)
Suntory Japan’s newest bottling facility, Shinano-no-mori Plant, is the production home for Tennensui mineral water, packaged in one of the lightest PET bottles in Japan. The bottles’ thinness increases quality risks during production, such as dents caused by contact between the filled bottles or bottles falling over.
For this brand-new plant, Suntory was seeking a product-handling solution for the filled water bottles that would prevent both sorts of damage and thus maximize both quality and productivity. Suntory settled on Sidel’s Gebo AQFlex compact, all-in-one conveying and accumulating system for its gentle, “100% contactless” and single-lane container handling. Although the system is not brand new (it was introduced in 2017), this is one of its most challenging applications due to the extreme thinness of the PET bottles.
The Gebo AQFlex system had already proved itself at Suntory France. The system is notable for its flexibility, suited to output from 1,000 to 100,000 bottles/hr. The system operates fully automatically at more than 99.5% efficiency, whatever the speed, according to Sidel. The Shinano-no-mori Plant bottles Tennensui mineral water in 550-ml and 2L bottles, but the system can easily handle additional formats, Sidel says. Changeover is done automatically, requiring no manpower.
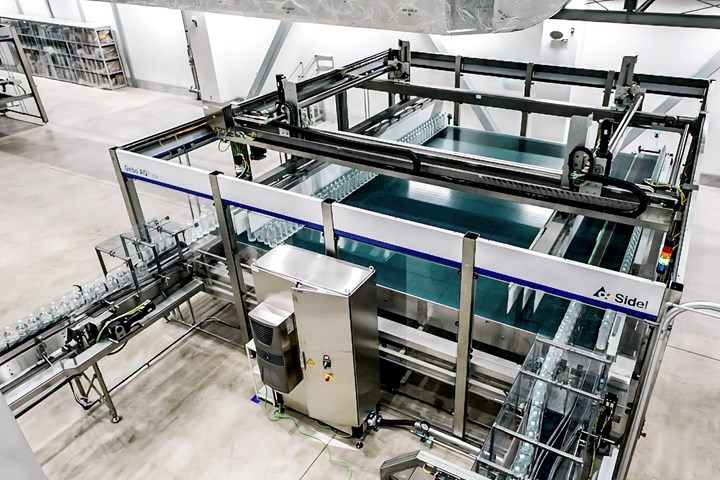
Sidel’s gentle, contactless, single-lane conveying with minimal curves protects ultralight PET bottles at Suntory Japan.
The installation at Shinano-no-mori Plant started during the COVID-19 pandemic, limiting the ability of Gebo AQFlex experts to visit the plant. However, they fully supported local Sidel technicians and Suntory teams by means of a remote factory acceptance test using Augmented Reality (AR) glasses and by providing 24/7 assistance during installation and commissioning. Once able, they visited the plant to fine-tune the machines and optimize efficiency. As sole production site for Tennensui mineral water, the plant must run 24/7 and Sidel’s remote support helped ensure the production line was never stopped.
Akihiro Fujiyama, general manager production for the plant, is impressed by the system’s “space-saving and simplicity of layout.” His team found the Gebo AQFlex system “attractive because it minimizes curves.” But “the best thing,” he adds, “is there’s no contact between the bottles.”
Related Content
-
PHA Compound Molded into “World’s First” Biodegradable Bottle Closures
Beyond Plastic and partners have created a certified biodegradable PHA compound that can be injection molded into 38-mm closures in a sub 6-second cycle from a multicavity hot runner tool.
-
Foam-Core Multilayer Blow Molding: How It’s Done
Learn here how to take advantage of new lightweighting and recycle utilization opportunities in consumer packaging, thanks to a collaboration of leaders in microcellular foaming and multilayer head design.
-
Get Color Changes Right In Extrusion Blow Molding
Follow these best practices to minimize loss of time, material and labor during color changes in molding containers from bottles to jerrycans. The authors explore what this means for each step of the process, from raw-material infeed to handling and reprocessing tails and trim.