Cold Deck for LSR Molding
After field testing, validation and refinement with customer feedback, Husky announced the introduction of a cold-deck system for direct gate molding of LSR.
Saying its design is based on decades of field experience with valve gating and material delivery technology in thermoplastic hot runners, Husky has launched a cold deck system for injection molding of liquid silicone rubber (LSR). While many aspects of its melt delivery expertise apply to LSR molding, there are some key differences, according to Husky. Derrick Hennebicque, product manager, hot runners at Husky, walked attendees of through the development in a presentation at the conference.
LSR processes in reverse as compared to thermoplastics, with melt delivery systems tasked with keeping the two-component mixture cool, while the cavity is heated to crosslink the LSR once material has been injected into the mold. To this end, one of the primary tasks of the cold deck is to keep temperatures inside the cold deck and its nozzles cooled.
Husky also notes that the material’s flow behavior is very different than typical thermoplastics, with an extremely low viscosity and the ability to flash into a clearance of just 1 µm. When molding LSR with a cold deck, chilled material is contained in cold plates, but the cavity is heated to cure the material, leading it to expand away from the cold deck’s operating position. Hennebicque says this means the assembled loads are greater than the operating loads, forcing users to think about expansion occurring across all three axes. This means loads on gates and nozzles aren’t the only ones to be considered. Molders must also think about plate and interface alignment, which will also experience differential expansion. All of this means the operating pitch, or the space between nozzles when running, can be different than the design pitch.
While cavity balance in a standard hot runner can be controlled thermally, Hennebicque says the cold deck individual cavity fill rates are managed mechanically. With its cold deck, the valve-pin position is individually adjustable to throttle relative flow through each nozzle. The tip uses contoured flow geometry to work in tandem with the valve pin for cavity balance adjustment. Hennibicque says balance is managed by controlling the open or back position of the valve pin, which modifies flow restriction and the flow rate relative to other gates in the system.
Hennibicque says Husky’s cold deck uses nozzles specifically designed for molding LSR with a water jacket actively cooling each nozzle for its entire circumference and length, ensuring thermal uniformity. Commercially available seals are used to keep water inside the cooling network, and a valve gate with conical or tapered shutoff maintains gate quality and acts as an adjustable valve for fine-tuning cavity balance. Each nozzle includes a thermocouple that can connected either to a controller or to a molding machine interface.
Hennibicque says the cold deck's tip assembly is preloaded into the cavity, so even as the cavity expands away from the nozzle, constant contact and the standard seals reduce any risk for leakage. Also, because there is constant contact, low conductivity material is used to minimize any heat transfer. Split-bolted manifolds are standard for Husky's cold deck, enabling easy access to LSR flow channels for maintenance.
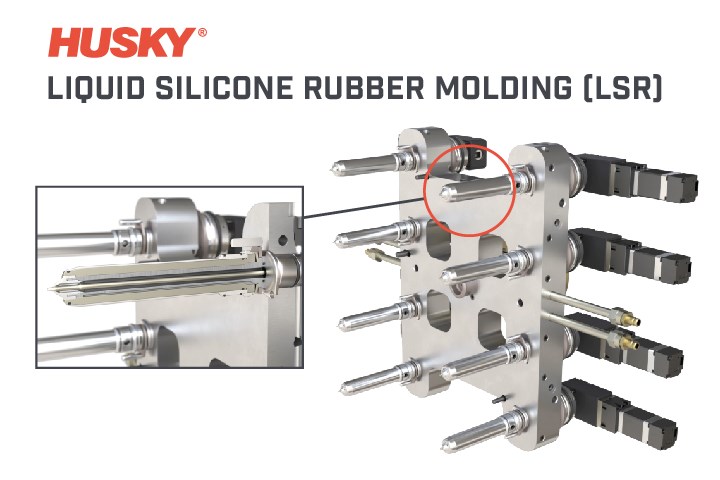
Husky’s new LSR cold deck applies the company’s knowledge of hot runner technology to the thermoset material. Photo Credit: Husky
Related Content
Optimizing Pack & Hold Times for Hot-Runner & Valve-Gated Molds
Using scientific procedures will help you put an end to all that time-consuming trial and error. Part 1 of 2.
Read MoreNew Hot Runner Temperature Control
Oerlikon HRSflow’s T-Flow HRS control has launched with three models that are configurable to multiples of six zones.
Read MoreConstruction Begins on Fully Automated Hot Runner Production Plant
Oerlikon HRSflow will start the construction of a new fully automated plant in San Polo di Piave, Italy, to expand capacity for the growing European market.
Read MoreHot Runners: Truths. Myths, Overlooked Areas: Part 2
Here’s a view from the trenches of a tooling manager who, over 30 years, has experienced the joys and pains of using virtually every type of hot runner on the market. Part 2.
Read MoreRead Next
Success in LSR Molding
Liquid silicone rubber parts are getting larger, but most LSR molders still have relatively small injection machines with limited shot capacity.
Read MoreHot Runners: Multi-Tip Nozzle For Vertical Gating, Process Monitoring and LSR Cold Runner
At K 2019, Ewikon will unveil a new nozzle range for vertical multi gating, process monitoring tech and a cold runner for LSR molding.
Read MoreBeyond Prototypes: 8 Ways the Plastics Industry Is Using 3D Printing
Plastics processors are finding applications for 3D printing around the plant and across the supply chain. Here are 8 examples to look for at NPE2024.
Read More