New Inspection Systems for Caps at K 2022
Improved separation and simpler inspection of tethered caps; cloud-based remote data access; new cap-tightening evaluation; and new sanitary washdown design.
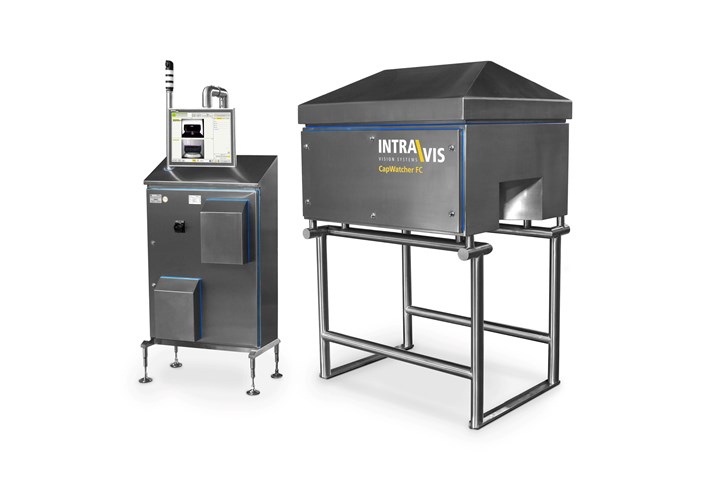
New Intravis CapWatcher FC, which uses index markings to check the degree of cap tightening by its angular position after application. The system also embodies the new sanitary washdown design. (Photo: Intravis GmbH)
At the recent K 2022 show in Düsseldorf, GmbH of Germany (U.S. office in Norcross, Ga.) introduced several new developments for inspecting caps, including the new tethered types. For the latter, Intravis presented an update to the CapWatcher Q-Line, which is tailored specifically to address the challenges of inspecting tethered caps, especially as the caps become thinner and thinner. What’s new is the way the closures are separated during inspection. In place of the previous star wheel used to separate the caps from above, a positive, form-fit lateral star wheel is said to ensure perfect separateion and positioning of caps, even at the highest speeds, while still handling them gently. New software avoids the need to align the caps, which simplifies the separation process.
The CapWatcher Q-Line shown at K was equipped with the new cloud-based version of the IntraVisualizer software for quality trend detection and analysis (available for all Intravis inspection systems). The cloud-based solution means that users do not have to maintain their own IT infrastructure to use IntraVisualizer; Intravis applies updates automatically. Customers also gain the flexibility to connect as many systems as they like, without capacity limits. And, the cloud solution allows display of all information on mobile devices.
Also new is the CapWatcher FC, which introduces a new inspection technology that uses index markings to inspect the angular position of the cap after application. With the help of five side cameras, the system detects whether the closure is screwed on in the target position or is screwed on too tight or not tight enough. The vision inspection system is guided by markings on the closure and neck support ring that are barely perceptible to the end user. The production-line operator receives statistics related to the average application angle with the capper’s tool, which allows malfunction of the tool to be detected quickly. In addition, CapWatcher FC inspects the bottle for damage, presence, and correct positioning of the closure, and records the fill level of the bottle.
CapWatcher FC embodies a new washdown design intended for systems that are located in the wet area of filling lines behind the filler. (The Intravis LabelWatcher inspection system is also available in the new washdown design.)
Related Content
-
Understanding the Effect of Pressure Losses on Injection Molded Parts
The compressibility of plastics as a class of materials means the pressure punched into the machine control and the pressure the melt experiences at the end of fill within the mold will be very different. What does this difference mean for process consistency and part quality?
-
Process Monitoring or Production Monitoring — Why Not Both?
Molders looking to both monitor an injection molding process effectively and manage production can definitely do both with tools available today, but the question is how best to tackle these twin challenges.
-
Hot Runners: How to Maintain Heaters, Thermocouples, and Controls
I conclude this three-part examination of real-world problems and solutions involving hot runners by focusing on heaters, thermocouples, and controls. Part 3 of 3.